Granite Glaze Tests - 2024 Year in Review
A review of glaze work completed in 2024 including lessons learned and future direction.
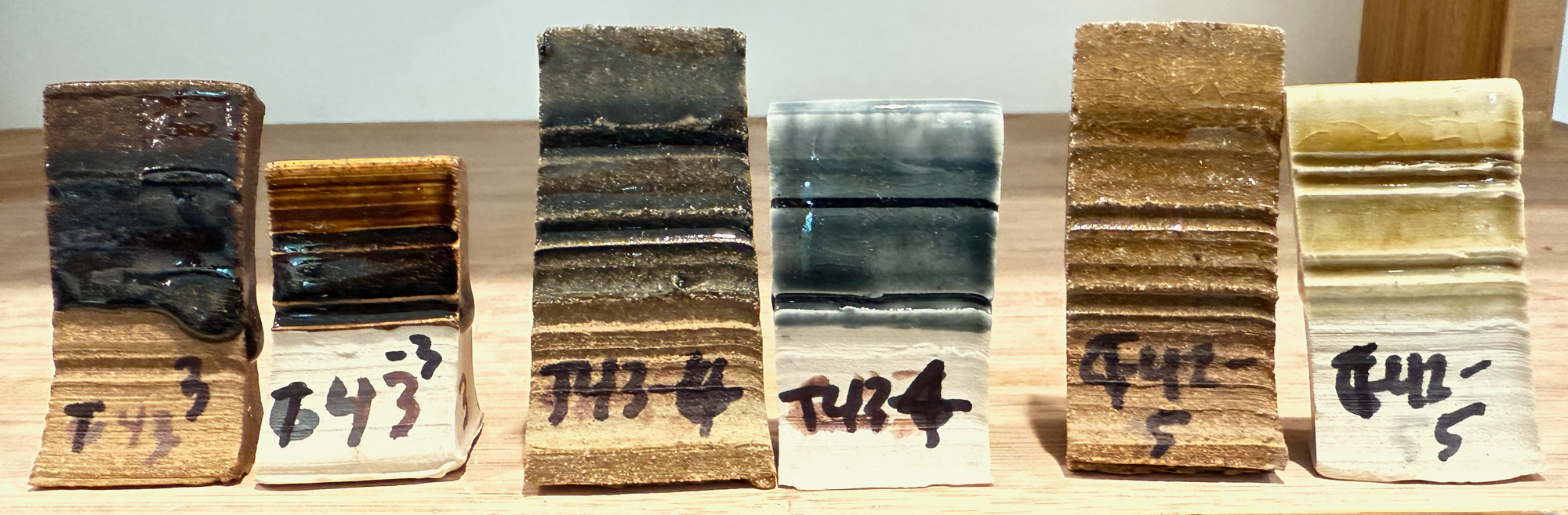
Testing of glazes using the Mt Vision Granite began Q1 2023 and continues to date, the results of which are documented in the blogs found on this site.
The final tests of 2024, conducted in September and presented below, drive a brief overview of conclusions to date. Overall, we are happy!
The tests cover 3 base glaze variations with no colorant and colorants Red Iron Oxide and Cobalt Carbonate. They are summarized below:
Base Glaze
Testing began initially in 2023 using a base glaze of 70% milled granite and 30% Wollastonite. This remains a viable starting point. Wollastonite adds more Silica and, more importantly, Calcium as a flux, making it a Calcium dominant glaze. It provides a functional glaze fired at Cone 6.
By itself the base glaze produces a honey matte color on white clay as the granite naturally contains ~4% iron oxide. It's generally less interesting on dark clay, but not always. The same is true when adding Cobalt Carbonate as a colorant. On white clay a nice grey-blue matte glaze is readily achieved. Adding Red Iron Oxide produces a melted glaze nearly every time and looks good on any clay. The micas in the granite provide interesting effects (Figure 1). Sieving the micas out (120M instead of 80M or 60m) makes the glaze more creamy and better melted.
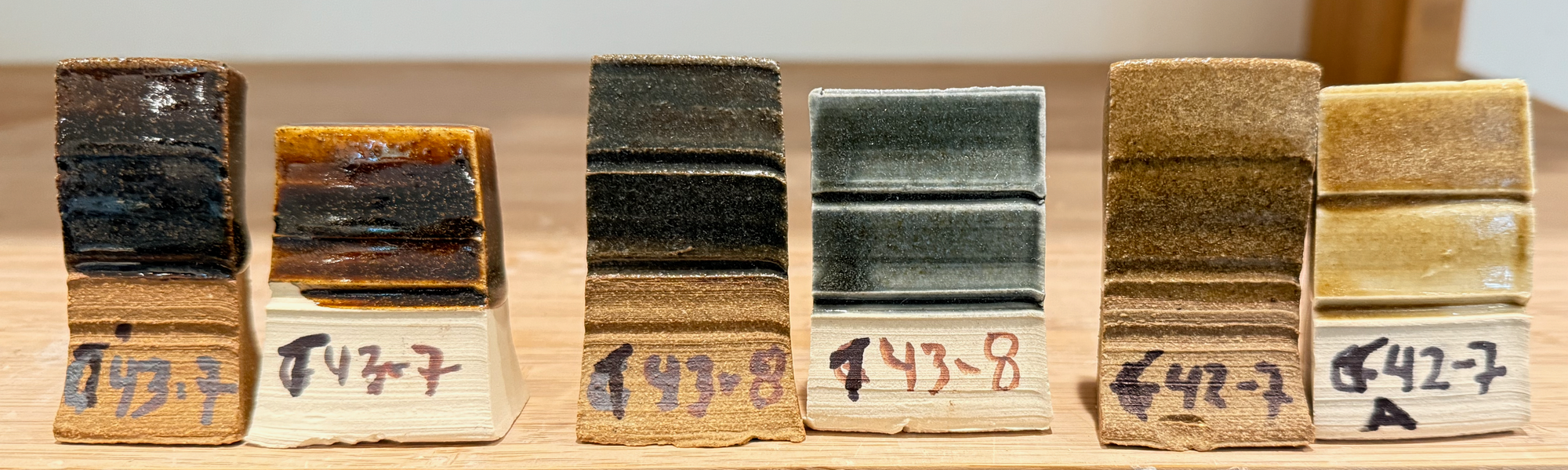
A common variation has been to add 10% Silica to the 70/30 base glaze mix above. This tends to give more results stable (than not adding silica). The results shown in Figure 2 are a bit more matte than those in Figure 1.
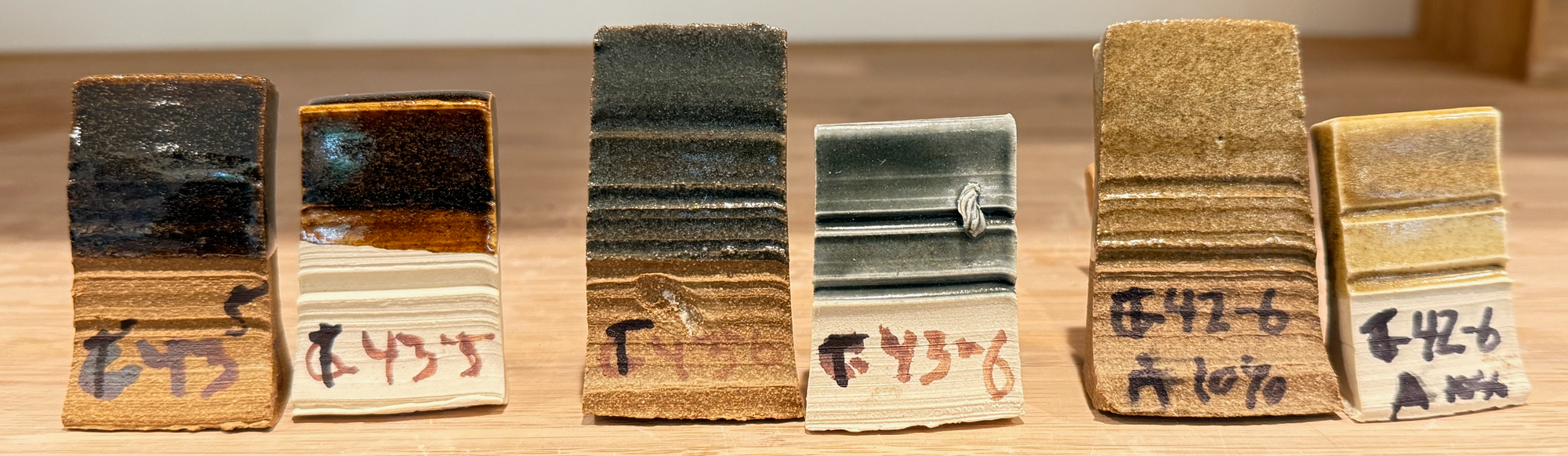
Adding Zinc Oxide as an auxiliary flux, instead of Silica, does move the needle from a matte glaze to a glossy glaze.
This took some time to realize, having become bogged down in analyzing milling techniques, kiln environments and so forth, but we are happy with it (Figure 3).
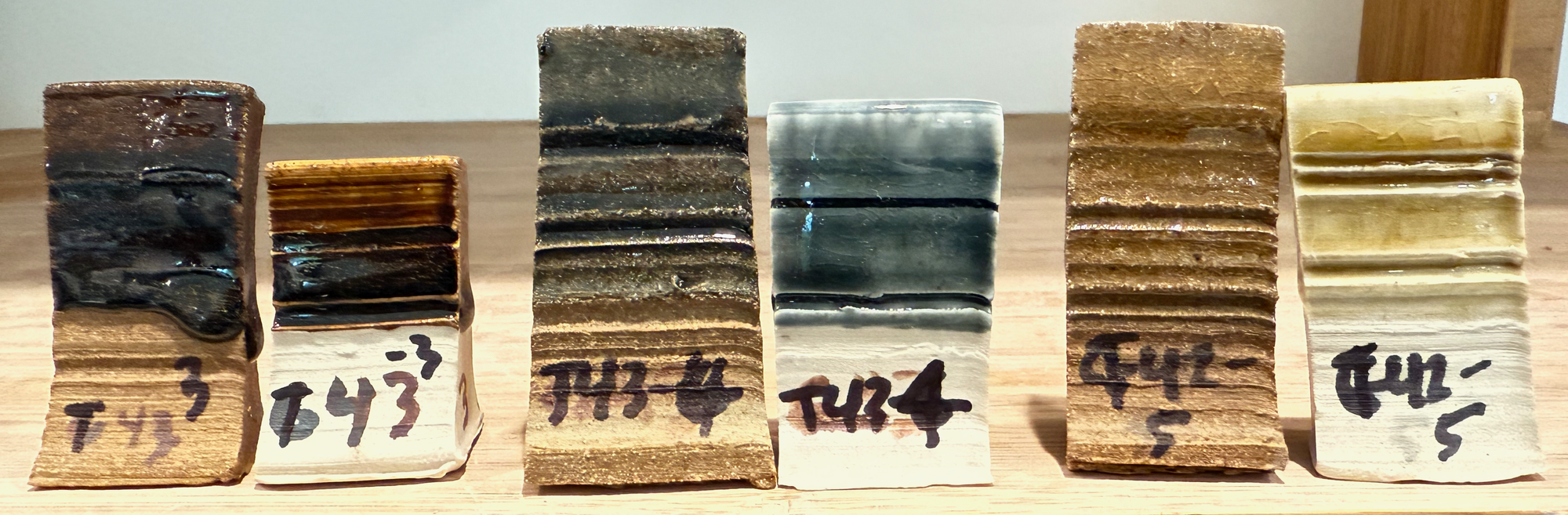
The Iron Oxide test (above) shows comparatively significant movement. The addition of Zinc Oxide does also melt the micas across the board without sieving!
Last quick test
Figure 4 shows the results of a last test I snuck in just before year end. A 2025 goal is to play with combinations of cobalt and other colorants. As I had left over glaze from the tests above, I added ~1% Iron Oxide to each of the Cobalt-based tests shown in Figures 1-3 (T43-8, -6, -4).
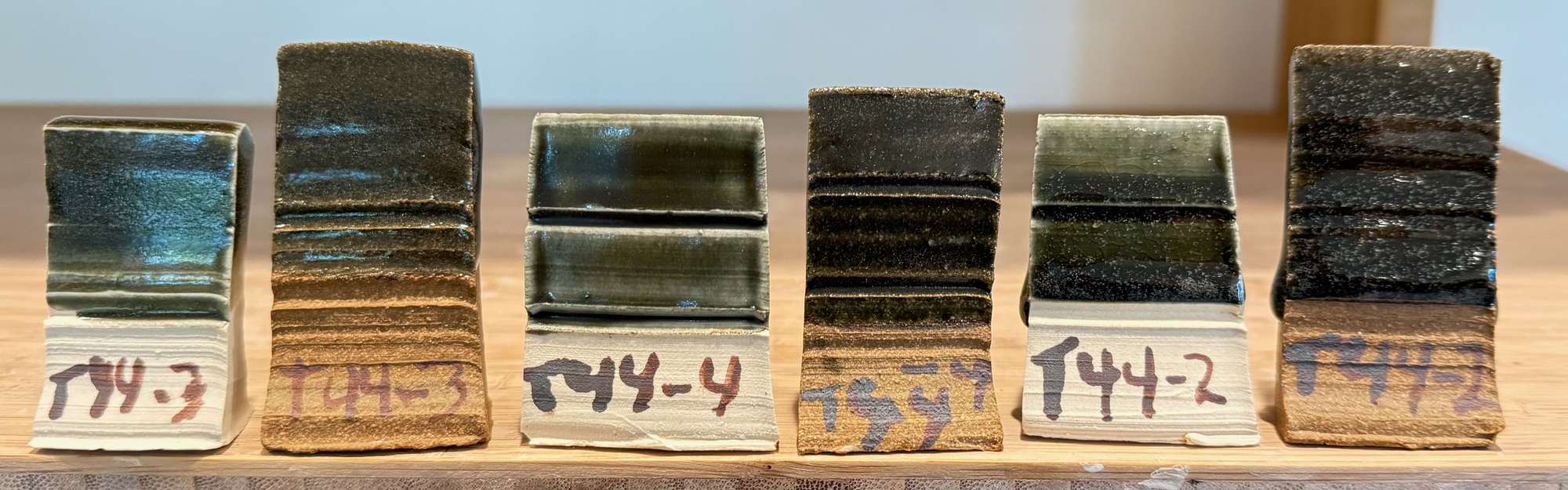
The first thing to notice is the blue turned to green across the board! This solves one of 2024's great mysteries where some batches of granite produced blue and others produced green. Now we know it's due to variations in the iron content of the granite! Phew. What luck!
And these are nice glazes, if you like green. The Iron Oxide adds a bit more flux to all examples, making them all a bit richer.
Summary
In summary the following concluding observations are offered:
- The base glaze (with or without the addition of silica) with no colorants consistently produces a yummy honey matte, especially when sieved to 120M and applied to a white body clay.
- The base glaze + 10% Silica and Cobalt Carbonate (0.25% - 2%) produces a nice matte blue that often is preferred to its glassy version obtained by adding 4% Zinc Oxide instead of 10% Silica. Muting the cobalt will be an interesting future experiment, as we saw in the final test above, adding iron oxide can produce greens instead of blues.
- When adding Red Iron Oxide as the main colorant, a good glaze is always achieved, but adding 10% Silica seems to be the sweet spot. Adding Zinc Oxide is not necessary, the iron oxide is clearly providing color and flux.
- Generally speaking, removing the micas through sieving improves the melt and reduces any particle roughness in the final glaze (which can be sanded). But the micas do add a nice effect to the final glaze, it's a trade-off. Adding Zinc Oxide will (help) melt the micas creating a more uniform glaze.
- Red Iron Oxide acts as a better flux than Cobalt Carbonate, all else being equal.
Also ...
Lot's of tests are not covered by the above summary but can be found in earlier blogs.
- For the record, we are aiming for a granite glaze that uses as much granite as possible, which seems to be in the 60% - 70% range when firing to Cone 6.
- Very quickly it was realized variations in rock selection for milling, the milling process and the final batch size from milling can produce a glassy or matte glaze. Later, it was realized matte was the more common outcome and the search was on to return to the elusive glassy early results (something that has not yet been definitively worked out apart from adding Zinc Oxide or Red Iron Oxide). Much work was devoted to this problem over the course of the year in which we established the following:
- The kiln environment in the test kiln and main kiln are essentially equivalent and stable.
- (1) rock selection for milling, (2) the milling process itself and (3) the ultimate batch size of milled granite influences the glaze produced.
- This indicates, among other things, that while the glaze may change from batch to batch, larger batch sizes will provide more stability.
- The amount of iron oxide can vary from batch to batch which will change the glaze characteristics (as we found producing sometimes blue, sometimes green when cobalt is used as the colorant).
- Sieving the glaze with different mesh sizes has an effect, with finer sieving removing progressively more of the micas and producing creamier and better melted glazes. We tested with 60M, 80M and 120M.
- Each new batch of milled granite will need to be retested to determine its particular characteristics (so bigger batch sizes mean fewer tests and more consistency).
- We accept a certain level of non-reproducibility is our reality and not our enemy. We have some control, but not total. Embrace it.
- We experimented a little with Copper Oxide and Titanium Dioxide and should do more as the results were intriguing, especially with the MVG Tenmoku + Titanium Dioxide producing an interesting caramel colored glaze.
- We need to perform a proper biaxial test for Silica and Zinc Oxide.
- A black can be produced by applying a Red Iron Oxide wash under the MVG Tenmoku.
- Finding an additive to soften Cobalt would be interesting to find
- Zinc Oxide 2-5% - Zinc oxide interacts with cobalt to produce a more transparent and softer blue tone, often referred to as a "robin's egg blue."
- Magnesium (Talc or Dolomite) - Magnesium can soften cobalt’s intensity and create more muted, pastel-like blues.
- Rutile / Titanium Dioxide 1-3% - These materials introduce variation and complexity, often creating softer, more variegated effects with cobalt. Rutile in particular can add warmer undertones and break up the uniformity of the blue.
- Tin Oxide / Zirconium Silicate 5-10% / < 15% - These opacifiers can tone down the intensity of cobalt by making the glaze more opaque and muted.
- Iron Oxide 1-2% - Adding iron oxide can shift cobalt’s blue toward more complex shades, such as teal or gray-blue. It reduces the starkness of pure cobalt. As we say, it moves the blue to green.
- Manganese Dioxide 0.5-2% - Manganese can blend with cobalt to produce richer, more subdued blues with a hint of purple or gray.
- Experiment with other fluxes instead of or in addition to Calcium and Zinc
In conclusion, we have developed a small quiver of stable granite-based glazes and in the process have established a standardization for milling and firing the granite. Now it's time to expand the quiver!