Granite & Cobalt Carbonate
Experiments with Cobalt
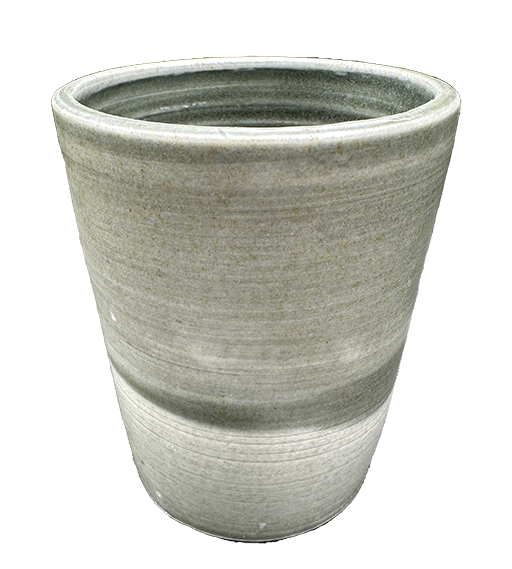
The following documents tests and results primarily using the Mt Vision Granodiorite and Cobalt Carbonate. More recent tests have added additional colorants to the granite + cobalt base mix.
Recipes
A matte and a glossy version has been formulated
"Pacific Blue" Matte
An ocean blue-green matte glaze that varies between blue and green depending on the amount of iron contained in a particular batch of milled granite. The effect of the iron is most prominent at lower concentrations of Cobalt Carbonate.
Material | Amount |
---|---|
Mt Vision Granodiorite | 64% |
Wollastonite | 27% |
Silica | 9% |
100% | |
Cobalt Carbonate | 0.25% - 2% |
Bentonite | 2% |
Glossy Zu Blue
Material | Amount |
---|---|
Mt Vision Granodiorite | 68% |
Wollastonite | 29% |
Zinc Oxide | 3% |
100% | |
Cobalt Carbonate | 0.25% - 2% |
Bentonite | 2% |
An ocean blue-green glossy version that fully melts and also varies between blue and green depending on the amount of iron contained in a particular batch of milled granite. The effect of the iron is most prominent at lower concentrations of Cobalt Carbonate. Using the current batch of granite, named Batch A, zinc is required to produce a glossy version.
Firing
Kiln firing procedures are described here.
Discussion:
The Blue vs Green glaze color issue diverted us into a series of control tests that were not planned, but were valuable in the end. Ironically, it was a separate, random test, one that directly added iron and cobalt together, that led to the answer, which is
"A milled batch of granite will have a varying amount of iron content that can affect the color produced with the same glaze formulation in the presence of cobalt."
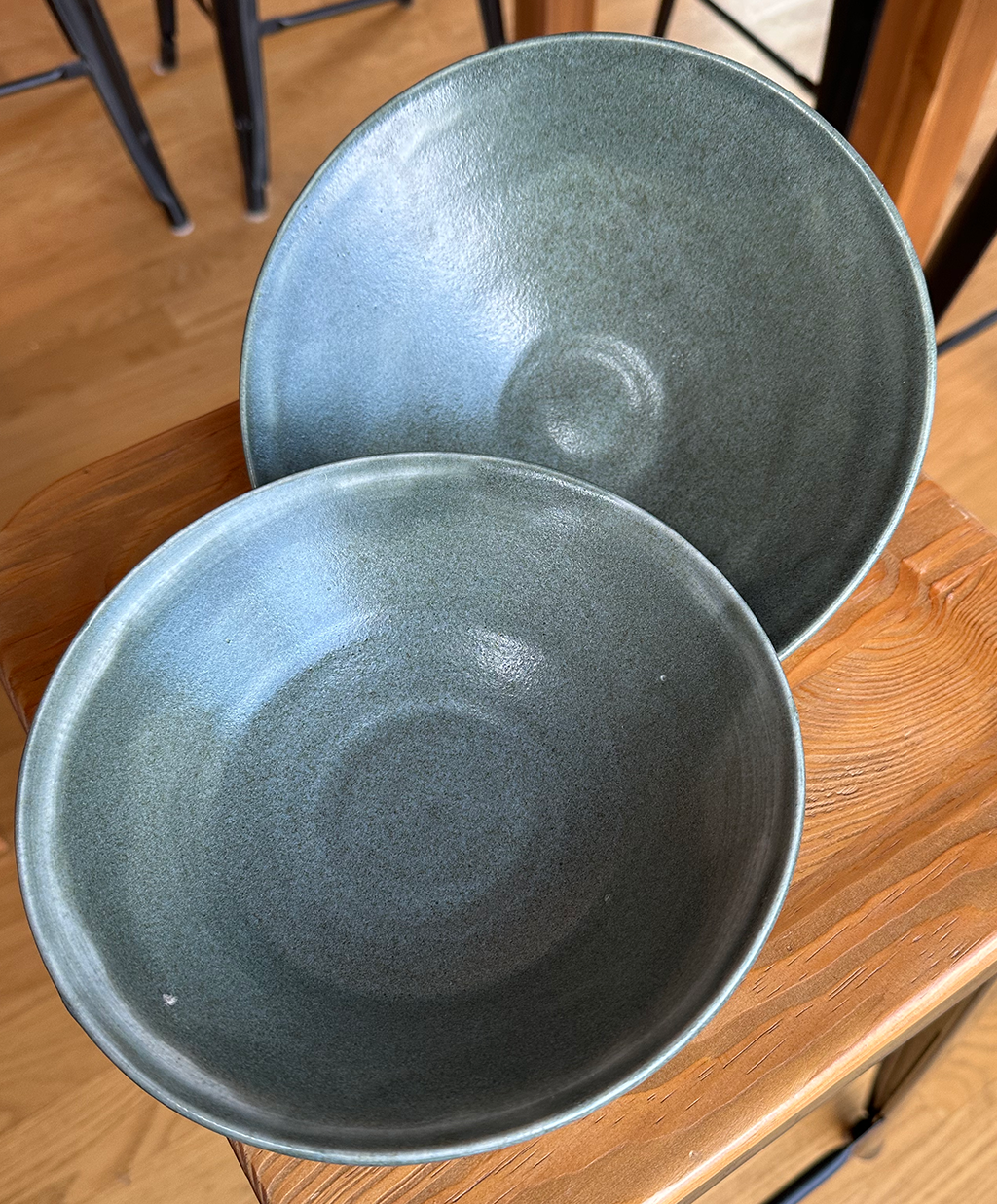
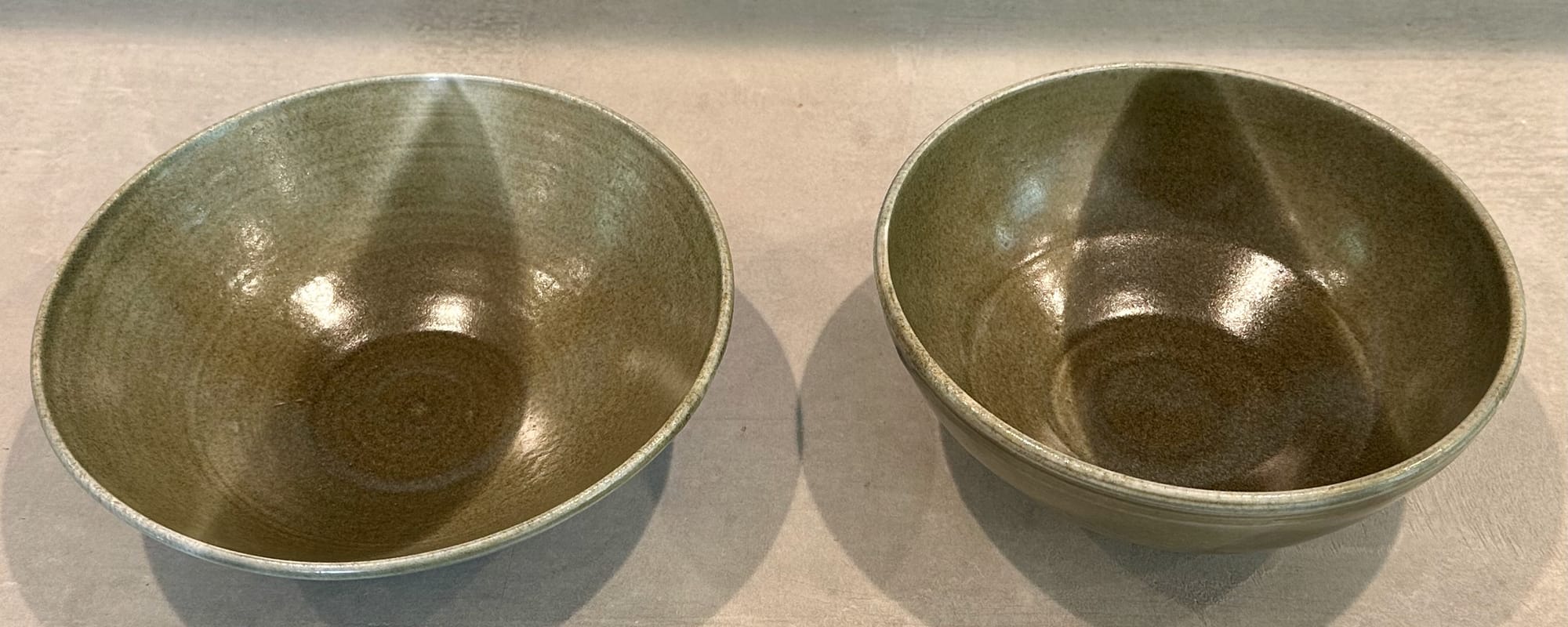
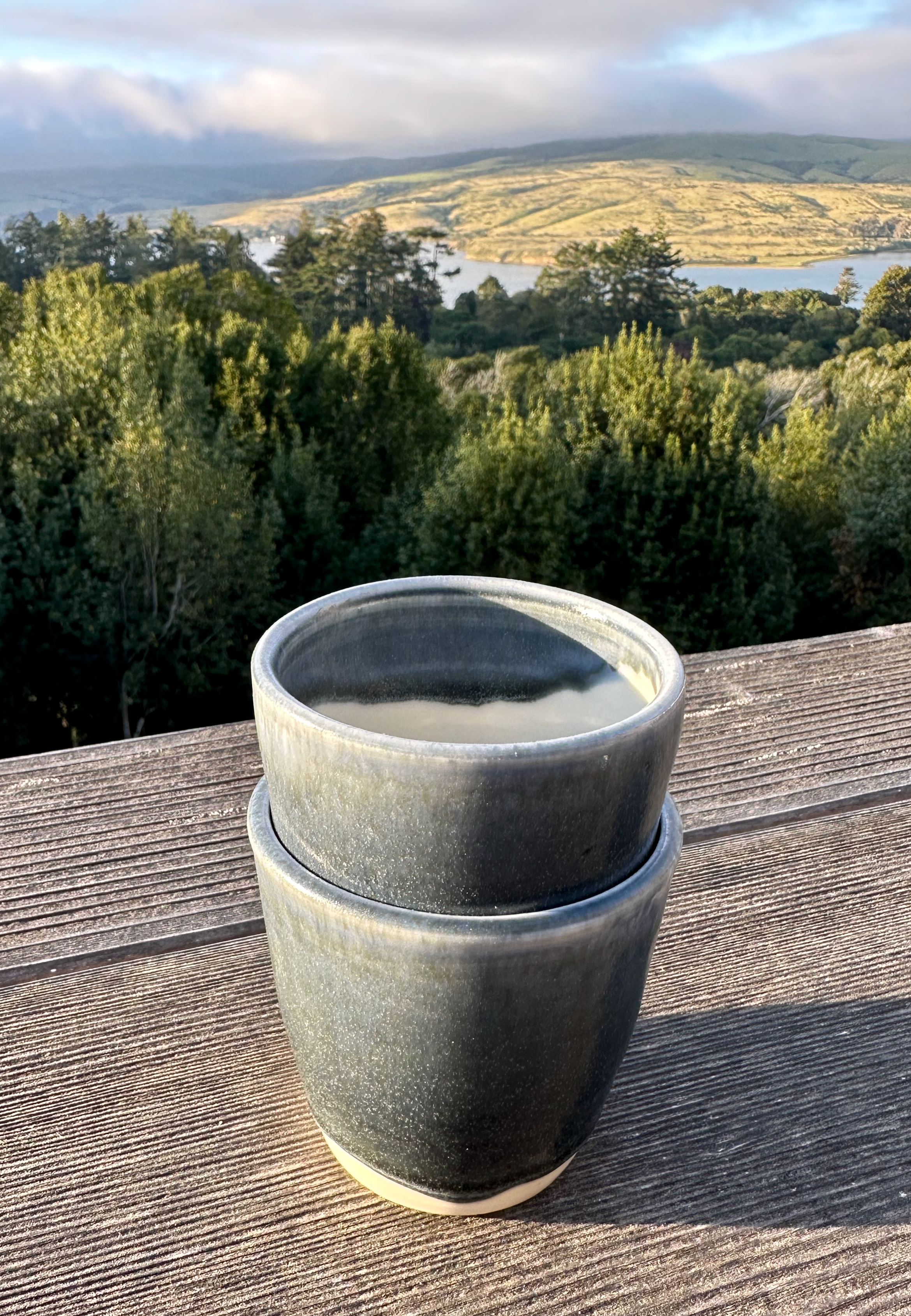
Left & Middle "Pacific Blue", 0.25% Cobalt Carbonate, different milled batches. Right "Zu Blue", 1% Cobalt Carbonate + 3% Zinc Oxide over FM Matte White.
The other issue we wrestled with was
"Why did the first batch of granite produce a glossy glaze while subsequent batches produced a matte glaze, all things being equal."
This we never quantitatively resolved and we can only conclude, again, that it is due to variations in the batches of milled granite. In the end we achieved a glossy version of the glaze by adding more flux in the form of Zinc Oxide named Zu Blue, after our Russian Blue cat ZuZeus.
So what drives the characteristics of a batch of milled granite? The first is rock selection, the second is milling technique and the third is the volume of material created for a given batch.
One might include a forth factor, being, the sieving of the final glaze, which will remove more of the micas from the glaze and which will make the glaze more uniform (fewer particles) and melt more easily.
So what did we learn?
- The Test and Main Kilns fire "identically" using the same firing schedule.
- We will pay more attention and document rock selection to see what we can learn over time.
- We have standardized the milling process through a series of tests that find a balance between under and over milling.
- We will make larger batch sizes to average out the variations in the rocks collected as best as possible. We will still have vacations from batch to batch, but perhaps they will be smaller, and each batch will last longer, yielding stable glazes for longer periods.
A final note on this topic. The discussion above mostly relates to glazes produced to date that use no colorant or use cobalt. When we use iron, to make a Tenmoku, for example, the glaze is much less fussy and nearly always produces a glossy glaze.
Tests
Test Synopsis
Most of these tests are centered on attempting to recreate the glossy glaze found in Test 1 and to understand the "Blue" vs "Green" phenominum. See the discussion above for an overview. Below each test is briefly described.
- Test 18: New Glaze - Zinc base with Cobalt and varying Tin Oxide: Very nice.
- Test 17: New Glaze - Zinc base with Cobalt and varying Chromium Carbonate: Bile
- Test 16: New Glaze - Zinc base with Cobalt and varying Talc. Interesting.
- Test 15: New Glaze - Zinc base with Cobalt and varying Rutile. Very nice.
- Test 14: Cobalt line blend with 3% Zinc oxide gets very close to Test 1 below, though rock selection is clearly a factor given the color differences between Test 14 and Test 1, especially for tiles 2 which show green versus blue.
- Test 13: Zinc Oxide shows promise as an additional flux.
- Test 12: Sieved to 80M from 60M, kept the residue. It was not as a dramatic improvement as for the iron oxide parallel. Residual was interesting. Need to return to the biaxle testing at 80M and more flux.
- Test 11: A large (3000g) batch of 0.25 Cobalt Carbonate MVG glaze came out green instead of the expected blue. Adding more cobalt brought the blue back, somewhat. The high levels of Mica in the latest glaze batches seems to be the reason for the green? And the matte vs glossy mystery? A next test should be to try to sieve out more of the micas.
- Test 10: Tried to match the granite with the granodiorite, chemically. Inconclusive. Two granite batches were tested with some small differences.
- Test 9: Large silica varation. Much like Test 8, unfired with high silica. Two granite batches were tested with some small differences
- Test 8: Varied silica and boron. The result was matte like Test 6. Two granite batches were tested without much difference.
- Test 7: Biaxiel Test, silica and alumina. The result was matte or underfired. Most perplexing.
- Test 6: Added silica. A different matte. Being fired in the test kiln, it provides another data point the kilns both producing matte glazes
- Test 5: Added 10% EPK. The result was less matte, but had some melt issues. On reflection, this was the best test in spite of an execution defect
- Test 4: Place two bowls in different locations within the main kiln to see if the results were sensitive to small differences within the kiln. They were not and came out identicle, and matte.
- Test 3: New batch of granite produces a matte glaze (Main Kiln - rules out difference between kilns)
- Test 2: New batch of granite produces a matte glaze (Test Kiln)
- Test 1: Line Blend produced glossy, semi-transparent glaze
Test 18
Date:02/19/25
Type: Line blend Zinc Base + Cobalt with Tin Oxide
Temp: Cone 6
Kiln: Test Kiln (T47-2)
Clay: B-Mix, Red Sedona, Mt. Vision Sienna Red
Method: Base glaze was 70 / 30 / 3% of MVG / Wolla / Zinc oxide plus 1% Cobalt Carbonate. Tin Oxide was varied 0%, 2.5%, 5%, 7.5% and 10%. 150 gm of dry material was mixed with 150 ml water making a glaze of SG ~1.5
A pure experiment, not expecting anything but to learn.
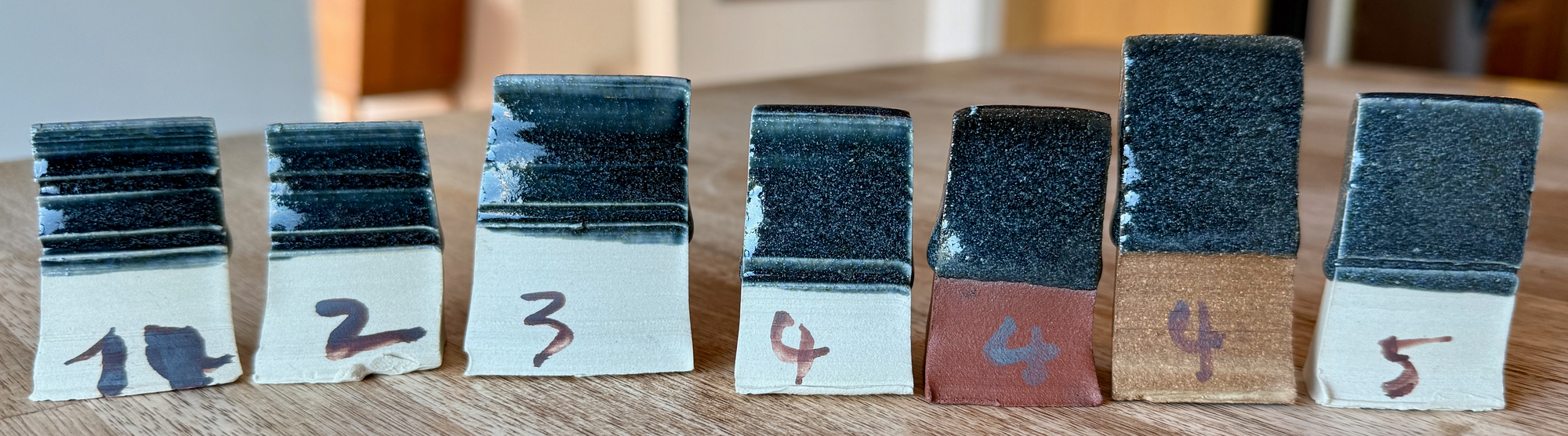
Notes
Also a fine result and worthy of further exploration.
Test 17
Date:02/19/25
Type: Line blend Zinc Base + Cobalt with Chromium Carbonate
Temp: Cone 6
Kiln: Test Kiln (T47-1)
Clay: B-Mix, Red Sedona, Mt. Vision Sienna Red
Method: Base glaze was 70 / 30 / 3% of MVG / Wolla / Zinc oxide plus 1% Cobalt Carbonate. Chrome was varied 0%, 0.5%, 1%, 1.5% and 2%. 150 gm of dry material was mixed with 150 ml water making a glaze of SG ~1.5
A pure experiment, not expecting anything but to learn.
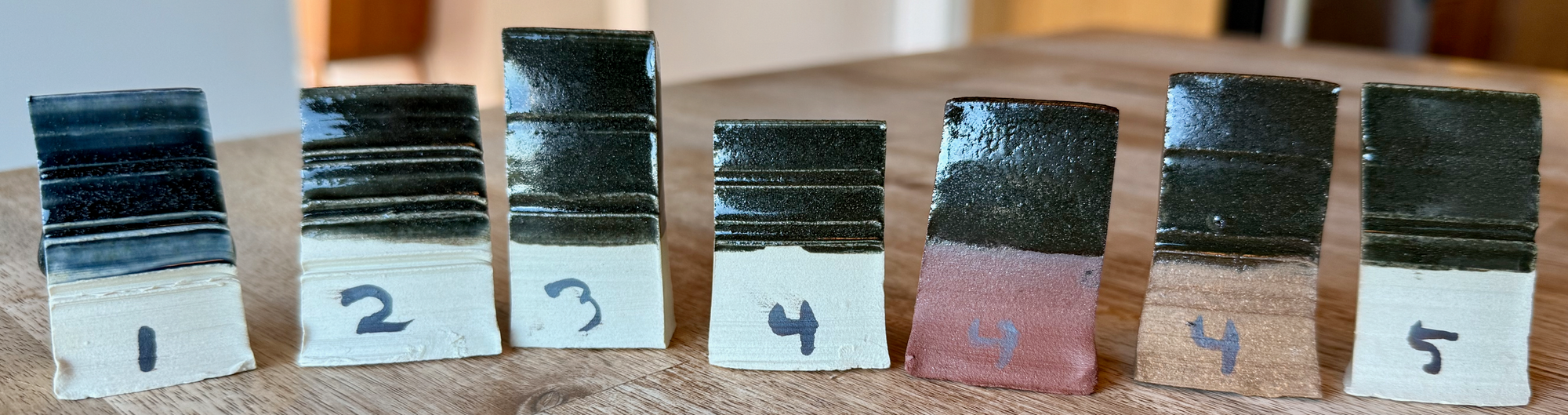
Note
Straight to blah. Nothing to see here. Good to know.
Test 16
Date:02/17/25
Type: Line blend Zinc Base + Cobalt with Talc
Temp: Cone 6
Kiln: Test Kiln (T46-2)
Clay: B-Mix, Red Sedona, Mt. Vision Sienna Red
Method: Base glaze was 70 / 30 / 3% of MVG / Wolla / Zinc oxide plus 1% Cobalt Carbonate. Talc was varied 0%, 1%, 2%, 3% and 4%. 150 gm of dry material was mixed with 150 ml water making a glaze of SG ~1.5
A pure experiment, not expecting anything but to learn.
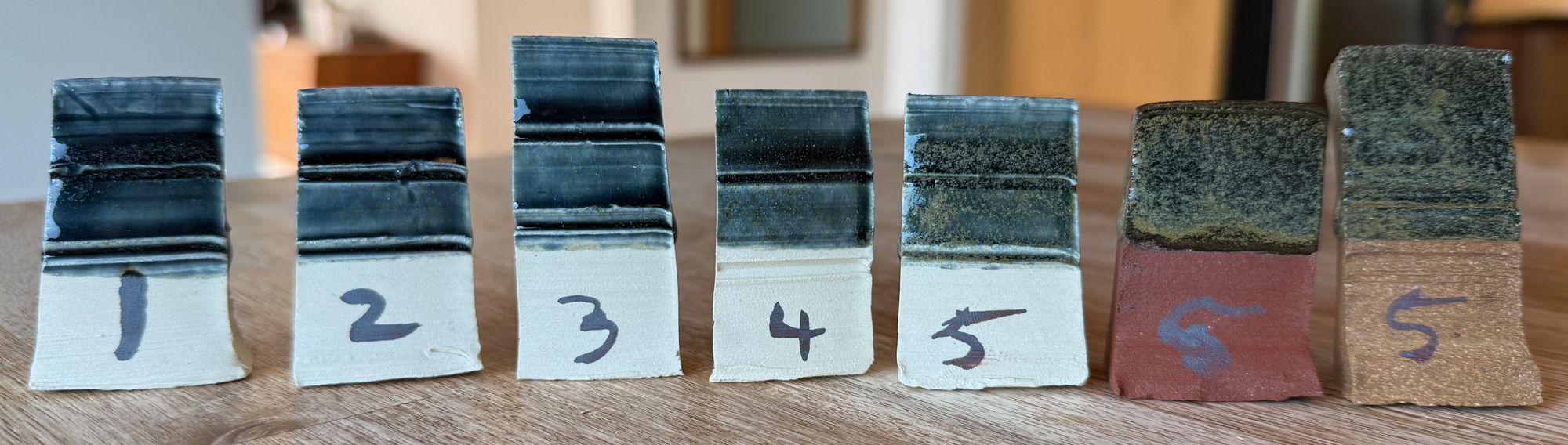
Notes
A fully developed variegated glaze with interesting features at 4% talc. Not sure how much I will develop it, however.
Test 15
Date:02/17/25
Type: Line blend Zinc Base + Cobalt with Rutile
Temp: Cone 6
Kiln: Test Kiln (T46-1)
Clay: B-Mix, Red Sedona, Mt. Vision Sienna Red
Method: Base glaze was 70 / 30 / 3% of MVG / Wolla / Zinc oxide plus 1% Cobalt Carbonate. Rutile was varied 0%, 1%, 2%, 3% and 4%. 150 gm of dry material was mixed with 150 ml water making a glaze of SG ~1.5
Seeking to explore different variations of cobalt carbonate. In this case also seeing if we can produce a variation of John Britt's John's Cash Cobalt Blue, a variegated blue glaze.
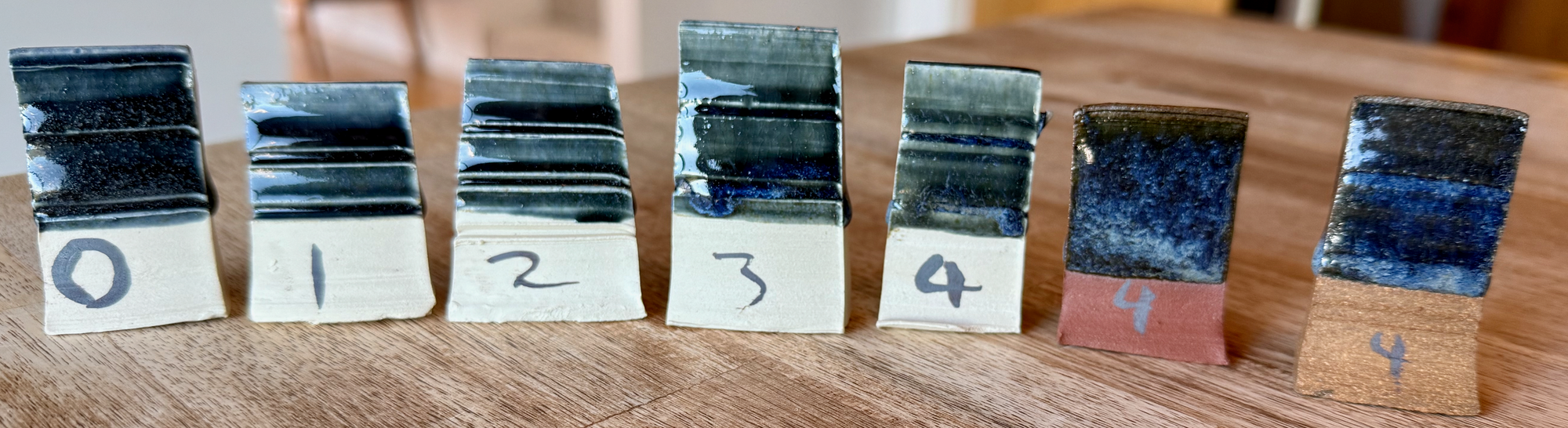
Notes
Good result at 4%. Is very much like John's Cash Cobalt Blue. This will be a useful glaze.
Test 14
Date:05/09/24
Type: Line blend Cobalt with a Zinc-based glaze
Temp: Cone 6
Kiln: Test Kiln (T40)
Clay: B-Mix, Red Sedona
Method: Base glaze was 70 / 30 / 3% of MVG / Wolla / Zinc oxide, using 12hr milled granite, SG ~1.5. Cobalt was then varied from 0, 0.25, 0.5, 1 and 2%.
The puropose of the test was to see how the cobalt line looked using 3% Zince oxide based on the results of Test 13 below. 3% was the point where the 70 / 30 mix of granite and wollastonite really melted.
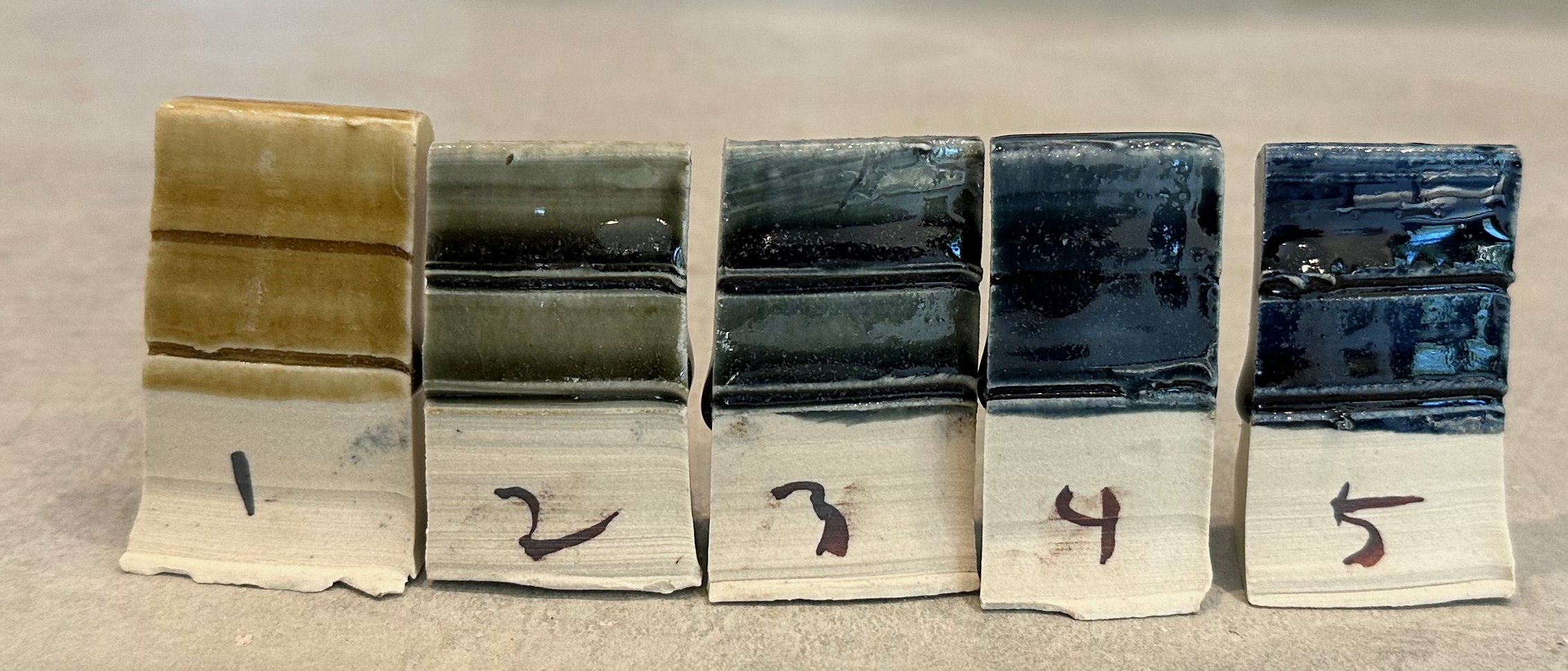
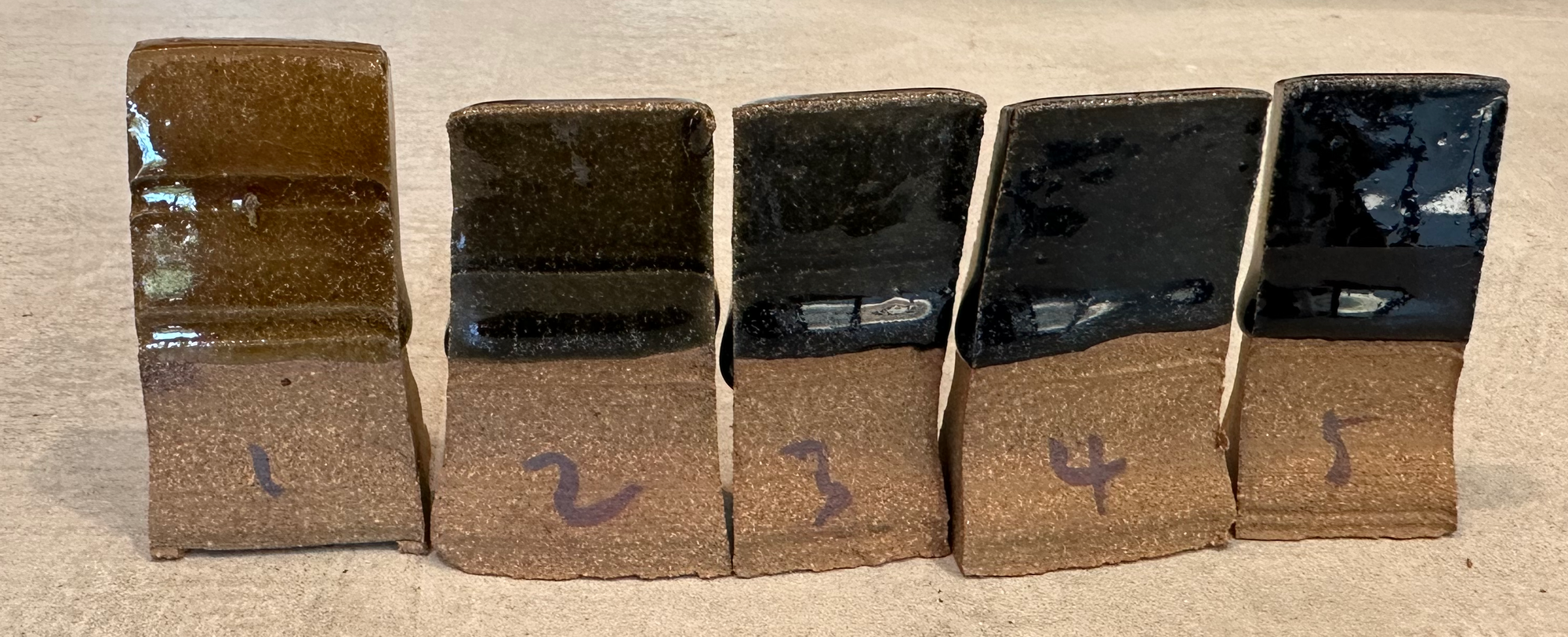
B-Mix left, Red Sedona Right
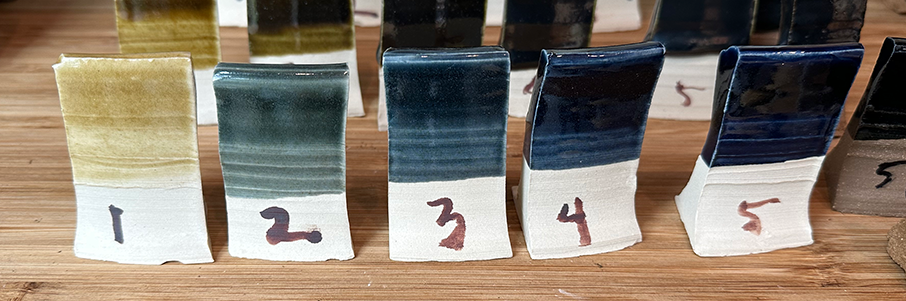
Notes
This is the closest yet in recreating the original glossy results of Test 1. But to do it, we needed to add Zinc oxide. Test 14 is a good result and deserves deeper exploration due the the following hypothesizes.
-
Rock selection for milling makes a bigger than expected difference. If the selection is concentrated with mica heavy samples, there will be more mica and the micas are not melting as readily. We see this in Test 13 where the addition of Zinc Oxide melts the micas.
-
12 hours milling may be too much and we are losing flux. One experiment comparing 6 hours versus 12 hour milling for the same rock selection shows a slight improvement in the melt for the 6 hour batch. But, milling less means much less passes through the 60M sieve and so the residue would further milling. An alternative would be to crush the granite more finely before milling and then milling for less time. This will need to be tested.
Test 13
Date:05/02/24
Type: Line blends with a new flux Zinc Oxide
Temp: Cone 6
Kiln: Test Kiln (T39)
Clay: B-Mix, Red Sedona
Method: Line blends of Zinc Oxide 0%, 2%, 4%, 6% and 8% with 70/30 MVG / Wolla + 0.25% Cobalt Carbonate + Zinc Oxide blend. Mixed 150 gm of material and added 150 ml of water which produced glazes of ~SG 1.5. No further sieving was performed, the 60M MVG was used.
Two glazes were mixed, one using the 12 hour, more recent milling batches that are dark and full of micas and the prior milling batch that is lighter with less mica (the processing was less well recorded).
I read Zinc Oxide is a good flux to bring the eutictic down in the Cone 6 range so I thought to try it.
The background is recreating a glossy cobalt glaze has remained elusive and recent batches of milled granite have more and more micas which has turned what use to be blue glazes to green glazes using 0.25% Cobalt.
It's feeling like rock selection before milling is becoming a bigger factor than hypothesized and implies a continuous variability in the end product unless some kind of standardization in selection can be obtain, which does not exist right now.
It also calls into question the milling process which will also have to be reanalyzed.
Regardless, for some time now, matte glazes have beem persistent and so this test seeks to determine the effects of the flux Zinc Oxide.
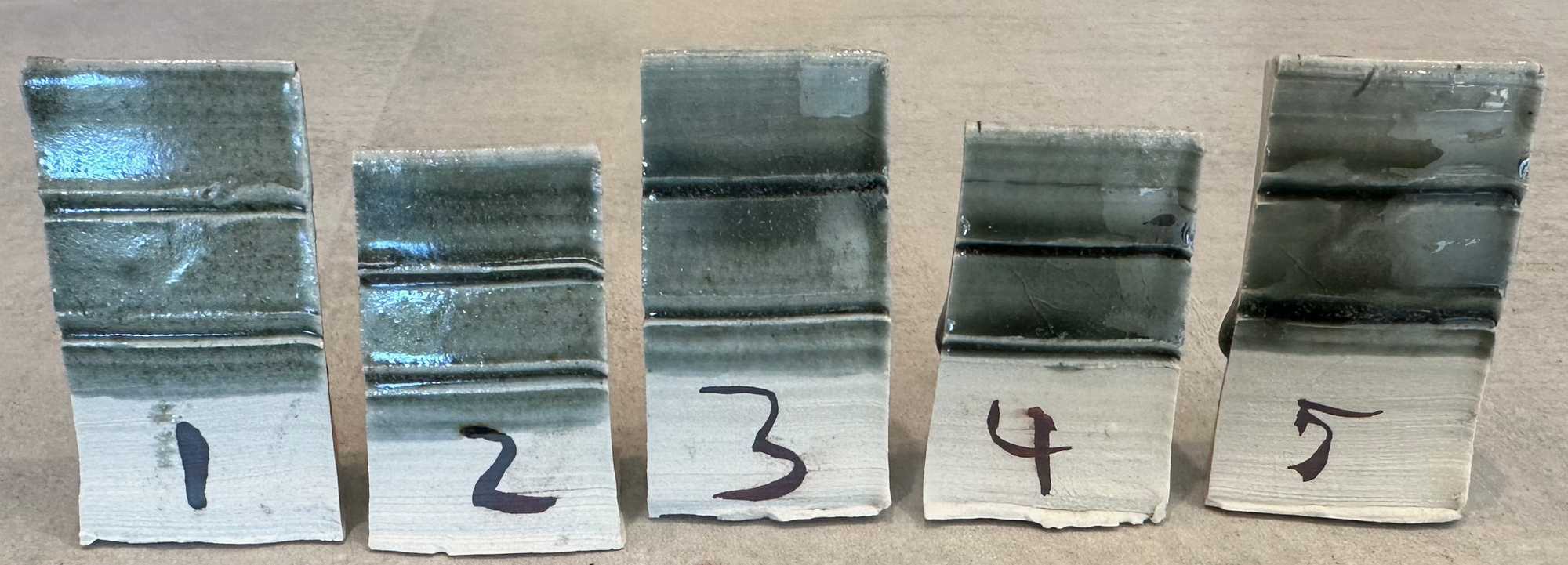
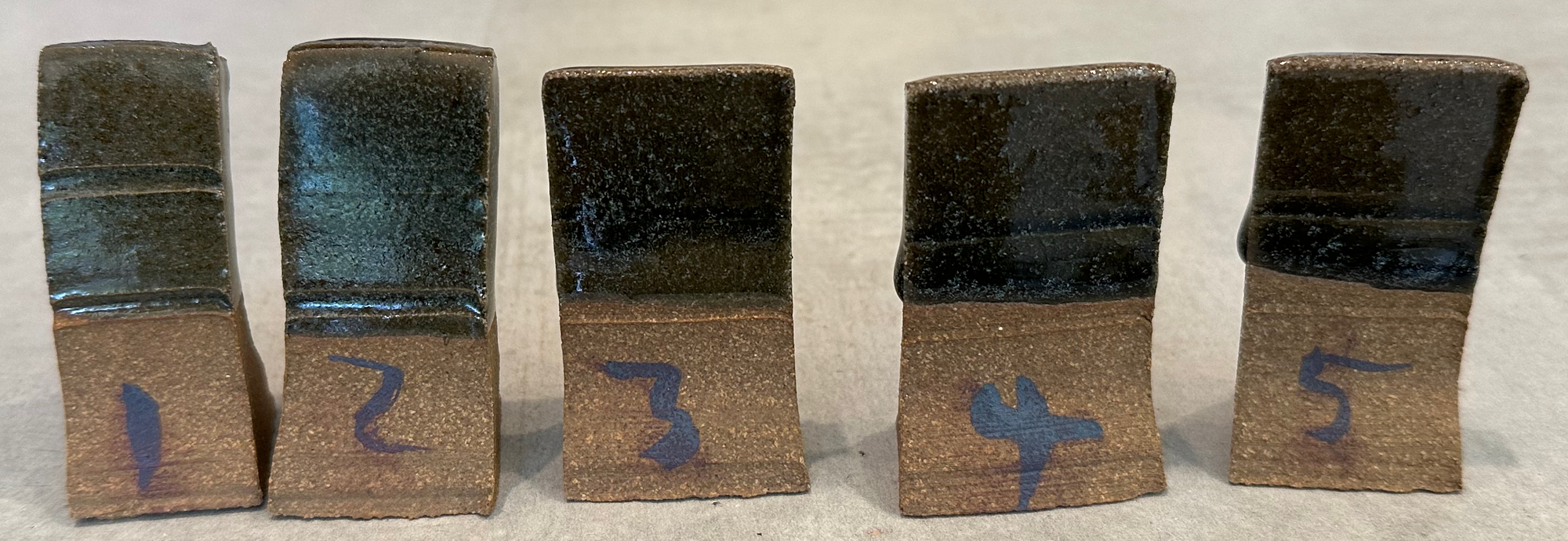
Line Blend of prior batch of milled granite that has less mica.
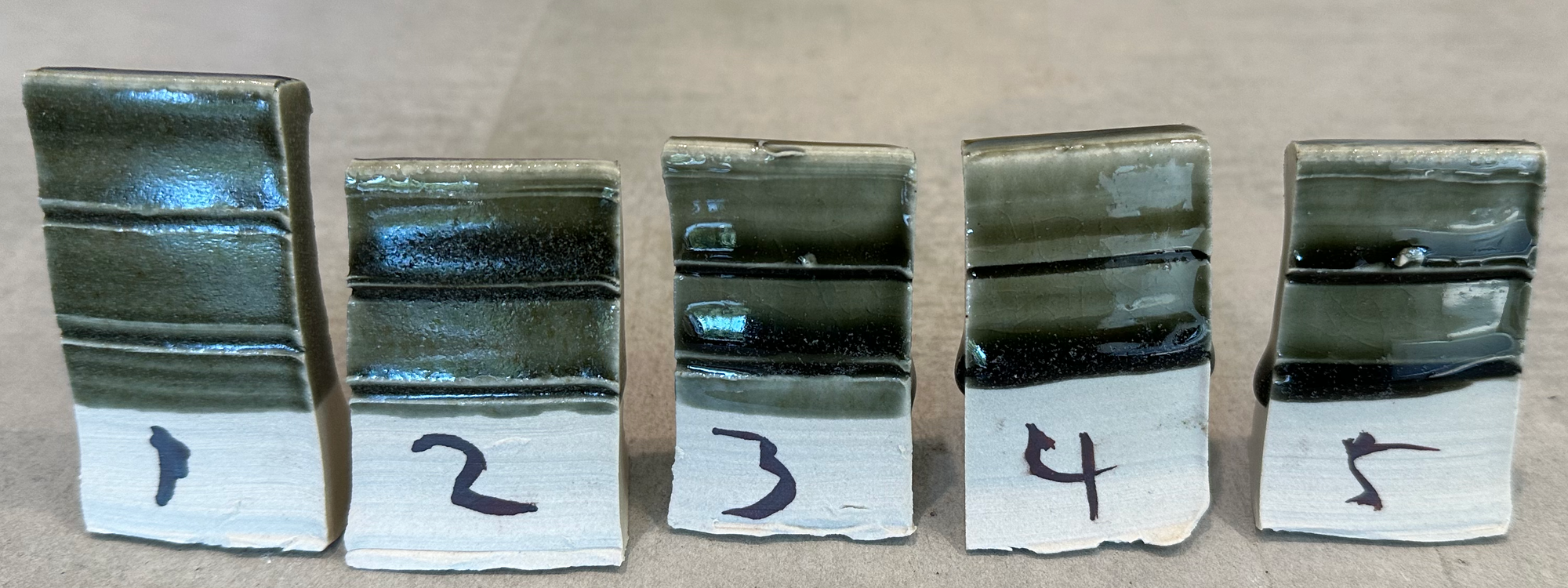
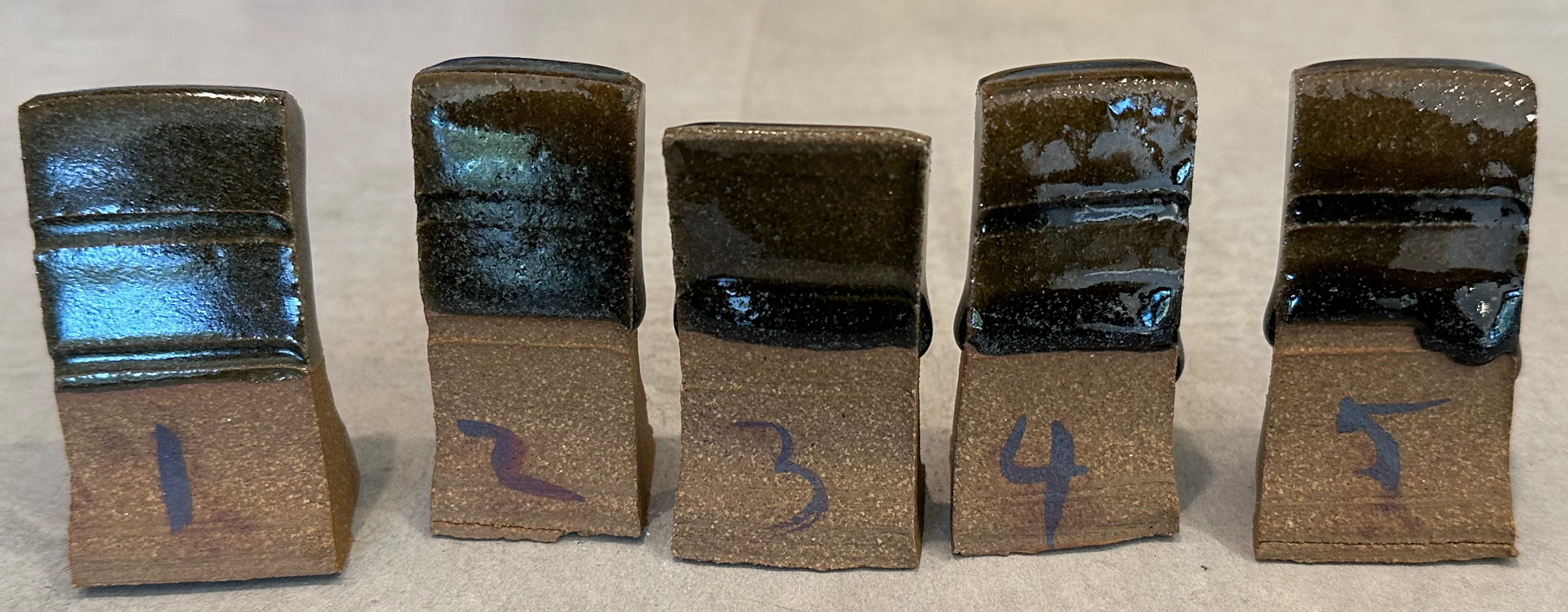
Line Blend of recent batch of milled granite that has more mica.
Notes
The Zine Oxide shows strong fluxing action and produced a glossy glaze starting at about 3-4% and continues to be more and more runny up to the final blend of 8%. Matte persisits less than ~3%.
When enough Zinc is presant, the mica yellow spots disappear (they melt).
Less mica in the milled rock produce a more blue glaze with 0.25% cobalt and more mica produce a green glaze, irrespective of the Zinc oxide content!
It seems the Zinc Oxide had a greater affect on the glaze with more mica (it's more runny and more glossy)
The one downside is all glossy tiles crazed.
This is an intriguing result and would imply more testing with Zinc Oxide is warrented. It's the first glossy glaze found since the early test.
Test 12
Date:03/23/24
Type: Sieve from 60M to 80M, see what the residue does
Temp: Cone 6
Kiln: Test Kiln (T37)
Clay: B-Mix, Red Sedona
Method: From the last large batch (Test 11) that was sieved at 60M, sieved it to 80M, and kept the residual.
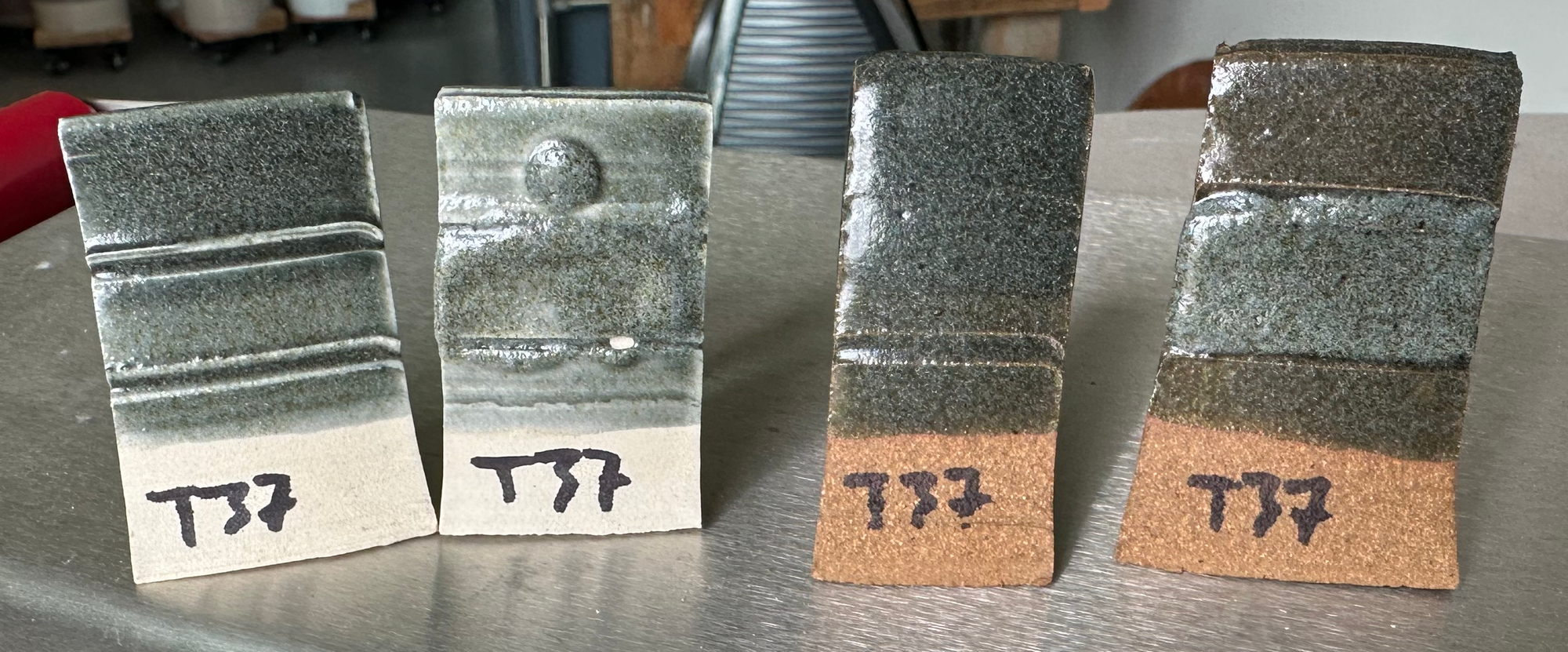
Notes
The left side of each pair above is the cobalt glaze at 80M that has been flocculated. It's comparible to the G44 tiles in Test 11 which was sieved at 60M and flocculated (see comparison below).
Frankly I don't see much of a difference, in fact I think any differences are do to the way I dipped them. I am starting to think that letting time micas settle after mixing might be an interesting approach? The flocculation did help improve the glaze consistency at SG 1.45. And the cobalt version might need more flux than it's iron oxide twin.
The right size is the same glaze over a strip of the residue from the sieving process painted in the middle.
And playing with the residue is interesting. Already a good result was obtained with the iron oxide version of the same experiement.
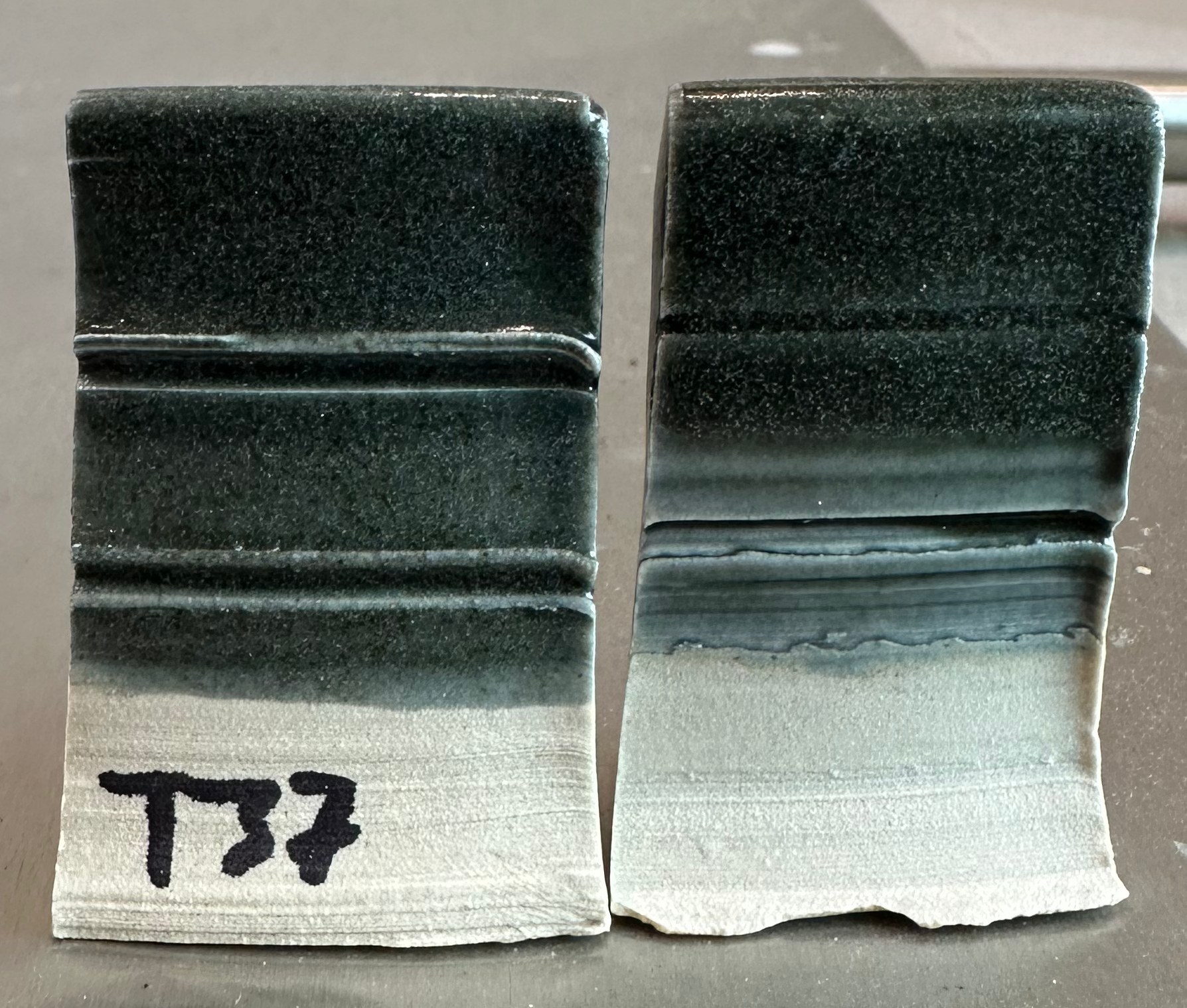
Test 11
Date:03/23/24
Type: Comparison of Test Tiles
Temp: Cone 6
Kiln: Test Kiln (T36), Main Kiln (G42, G43, G44)
Clay: B-Mix, Red Sedona
Method: Made a first large 3000g batch of the formula below.
The recipe is 64% MVG / 27% Wollastonite / 9% Silica + 0.25% Cobalt Carbonate and 2% Bentonite which corresponds to Tile 3 in Temoku Test 9 below.
I was expecting the usual blue and instead got GREEN?
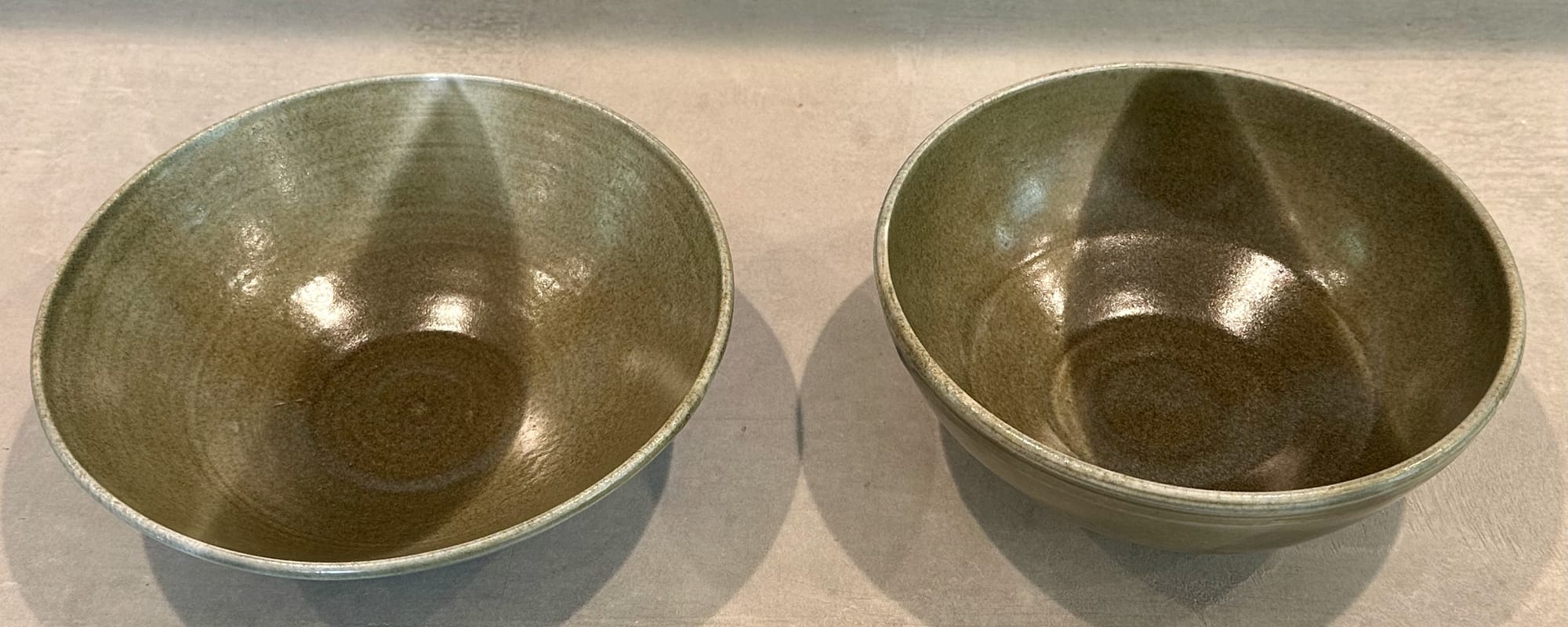
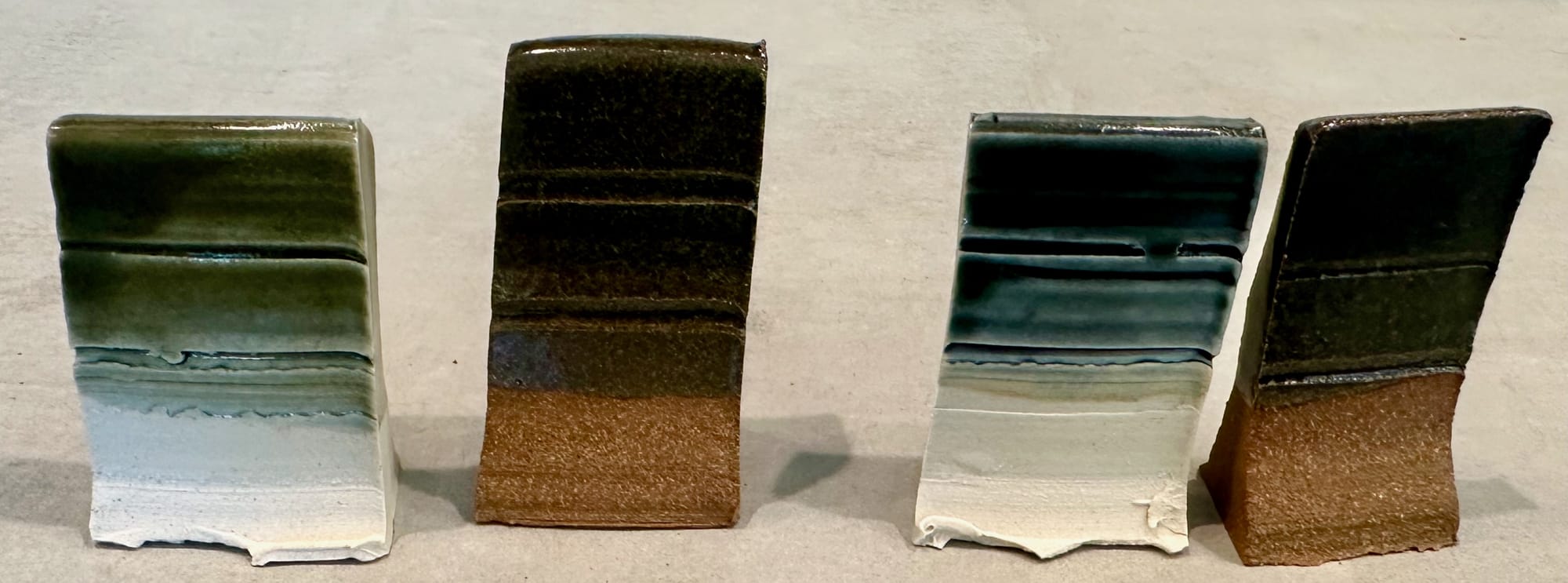
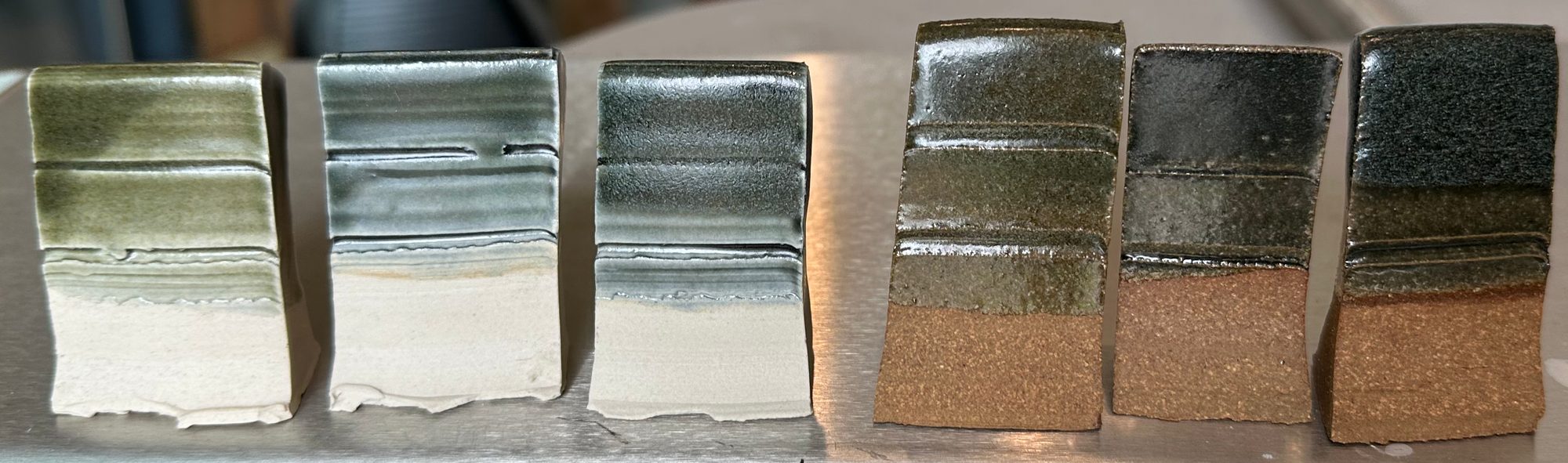
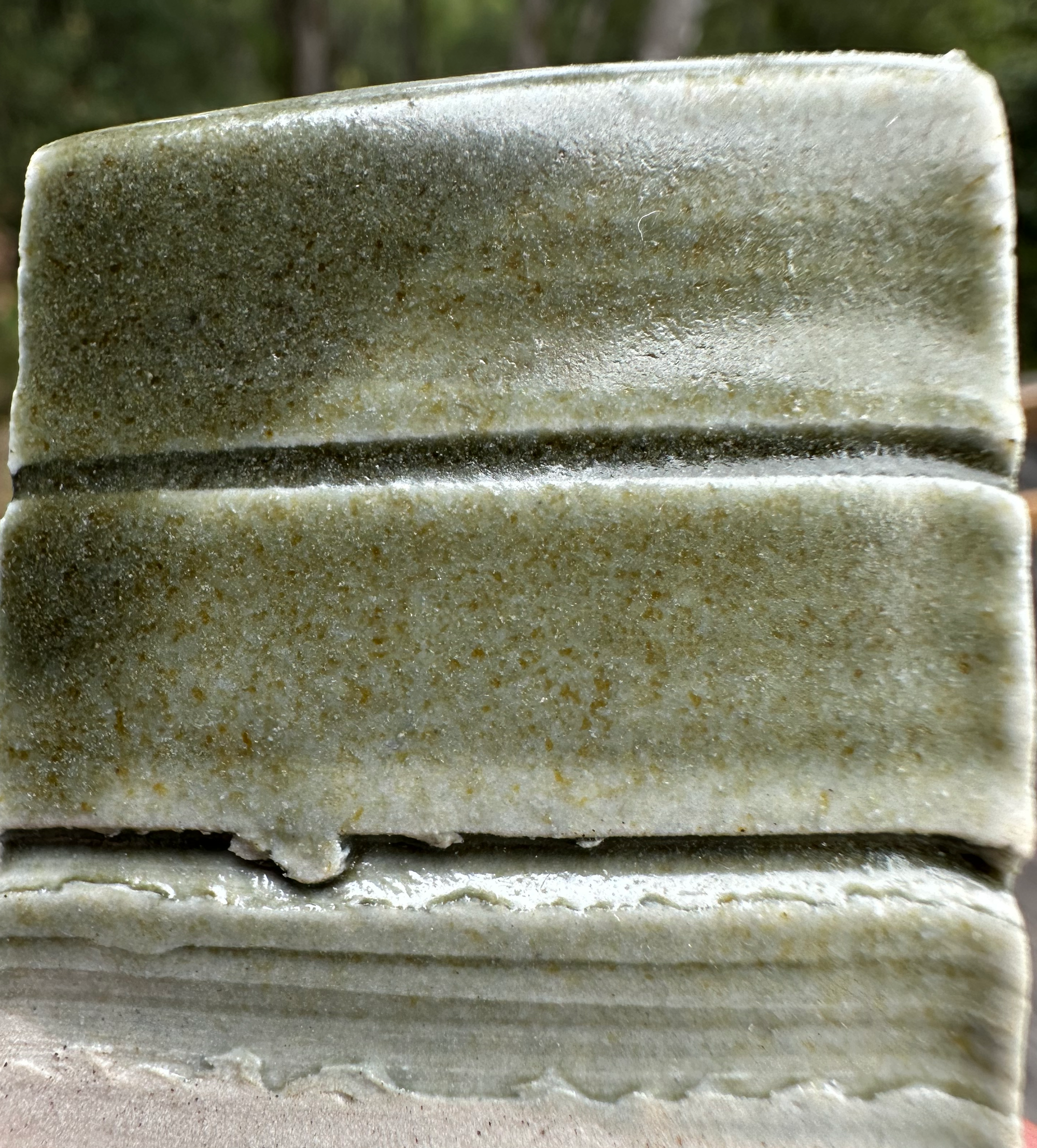
Notes
Well this was certainly an unexpected result!
The progression was, T36 test tiles were green, but I probably didn't notice initally, then the ware in G42 were obviuosly green. So I added more cobalt to see what happened and a more blue glaze returned in the G43 tiles. G44 is G43 with Epson salt added as a flocculant and it did improve coverage of the glaze.
Why Green?
The latest batches of milled granorite are darker and contain more mica in them than prior batches.
After some pondering I think this is the source of the "problem" after looking more closely at the details of the glaze (above). The micas are showing up as flakes of yellow-brown. Blue can be seen where there is less of the mica.
Sieving more of it out might help return the blue and make for a better melt (like the iron oxide results).
Milling longer could work towards the same ends, but has risks of over milling (and 12 hours is already a long mill).
ChatGPT says:
Yes, an abundance of mica in a glaze formulation can contribute to a rough, uneven, or matte glaze surface. Here's how:
Texture and Unevenness: Mica particles, particularly if they are larger or not well-dispersed in the glaze, can create localized areas of texture or roughness on the glaze surface. These areas may not fully melt during firing, leading to an uneven surface texture.
Matte Appearance: If the mica particles do not fully melt or if they promote the formation of crystalline structures during firing, they can contribute to a matte or satin finish on the glaze surface. Matte surfaces often result from light scattering caused by surface irregularities or crystalline phases within the glaze.
Test 10
Date:01/22/24
Type: Line Blend
Temp: Cone 6
Kiln: Test Kiln (T35)
Clay: B-Mix
Method: And now for something completely different ...
In the quest for reproducing Test 1 it occurred to me to try to chemically mimic the granite (versus the granodiorite). The idea was to reduce the calcium and increase the silica and match a 70/30 granite/wollastonite formulation.
Using glazy.org a 70/26/10 (66/25/9 normalized) granodiorite/wollastonite/silia formulation provides a reasonable match.
The Seger Unity comparison is provided below.
Rock | R2O:RO | Alumina | Silica | Ratio |
---|---|---|---|---|
Granite | 0.21:0.79 | 0.27 | 3.44 | 1:12.7 |
Granodiorite | 0.2:0.8 | 0.31 | 3.47 | 1:11.1 |
The line blend consisted of progressively adding cobalt producing a 0%, 0.25% 0.5%, 1% and 2% set of test tiles. To start 100gm of material was mixed in a cup with 125 ml of water.
Performed 2 tests, one with the original milled granite that mixed Granodiorite and Granite and the second with the latest milled granite that is just Granodiorite.
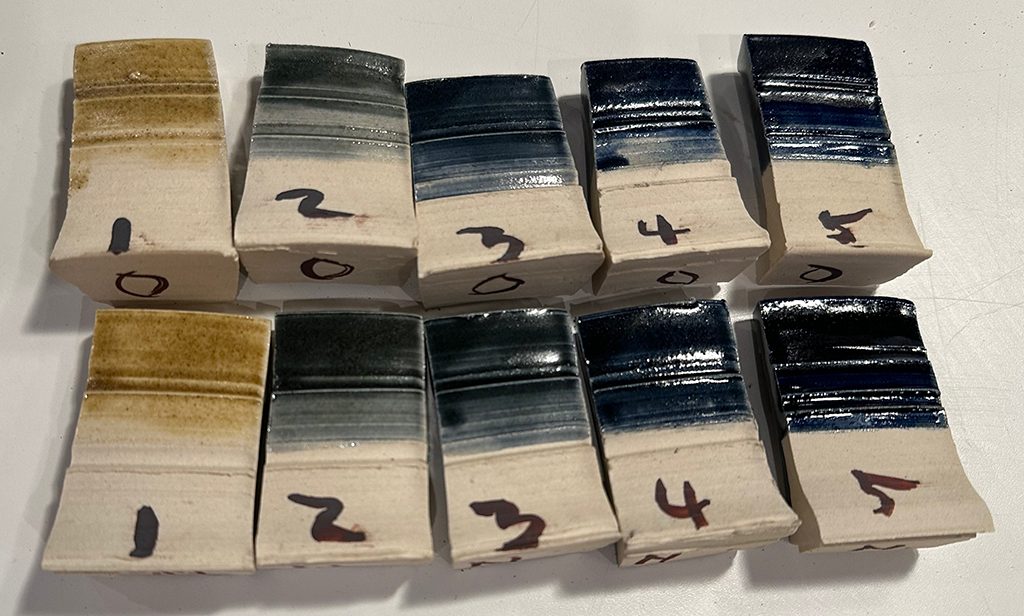
Notes
A shot in the dark that didn't produce.
The glossy tile remains elusive. The prior milled granite was noticibly underfired compared to the latest batch, which I would classify as matte again. And again the latest milled batch (foreground) was a darker blue than the prior batch. So the composition of the milled batches is enough to make differences in the resulting glazes. We saw this in the prior T34 test as well. This implies the more I can regularize my collecting and milling processes, the more consistent my glazes will be, and bigger batch sizes will help as well.
Test 9
Date:01/20/24
Type: Line Blend
Temp: Cone 6
Kiln: Test Kiln (T34)
Clay: B-Mix
Method: Line blend to test a more extreme variation of Silica. In search of a glassy and transparent glaze (like Test 1) and also to compare the milled granite batches as I hone my methods.
Cup A: 70% Granodiorite, 30% Wollastonite, 0.5% Cobalt
Cup B: Cup A + 30% Silica (normalized recipe before mixing)
Mixed 100gm of material in each cup with 125 ml of water.
Performed 2 tests, one with the original milled granite that mixed Granodiorite and Granite and the second with the latest milled granite that is just Granodiorite (see photo below). They were so different visually I thought to test them.
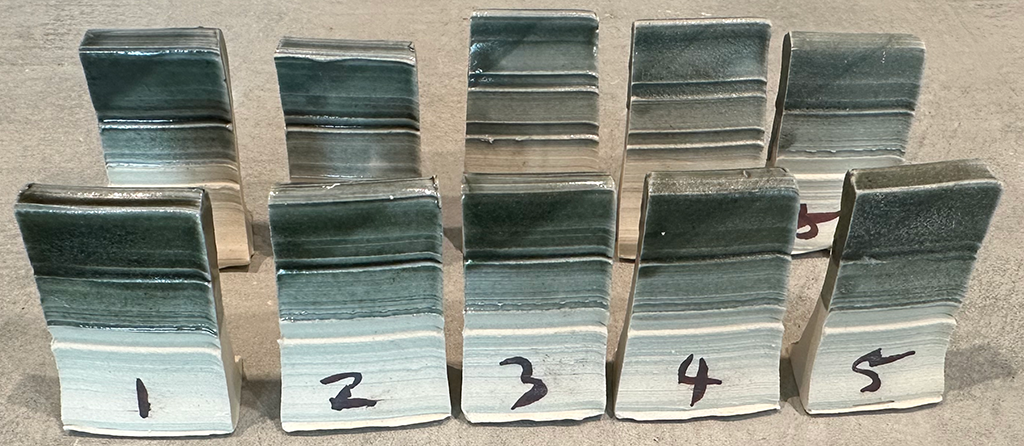
Notes
A somewhat unrevealing test as more matte variations were attained. The 30% addition of silica was a big overshoot into the underfired territory as seen on tiles 4 and 5 (not surprisingly). There is no appreciable difference between tiles 1 and 3 from a silica stand point (not so with similar test of the Tenmoku).
There was a noticible color difference between the milled batches with the newly milled granite (foreground) being darker. At this point, with respect to reproduction Test 1's result, I think I have nearly exhausted this avenue.
On the other hand, the matte is nice and can be used.
Test 8
Date:01/16/24
Type: Line Blend
Temp: Cone 6
Kiln: Test Kiln (T33)
Clay: B-Mix, Red Sedona
Method: Line blend to test variation of Silica with some Boron added for kicks (via Frit 3134). Via a small perturbation, in search of a glassy and transparent glaze (like Test 1) and also to compare the milled granite batches as I hone my methods.
Cup A: 70% Granodiorite, 30% Wollastonite, 0.5% Cobalt
Cup B: Cup A + 5% Silica, 5% Frit 3134 (normalized recipe before mixing)
Mixed 100gm of material in each cup with 125 ml of water.
Performed 2 tests, one with the original milled granite that mixed Granodiorite and Granite and the second with the latest milled granite that is just Granodiorite (see photo below). They were so different visually I thought to test them.
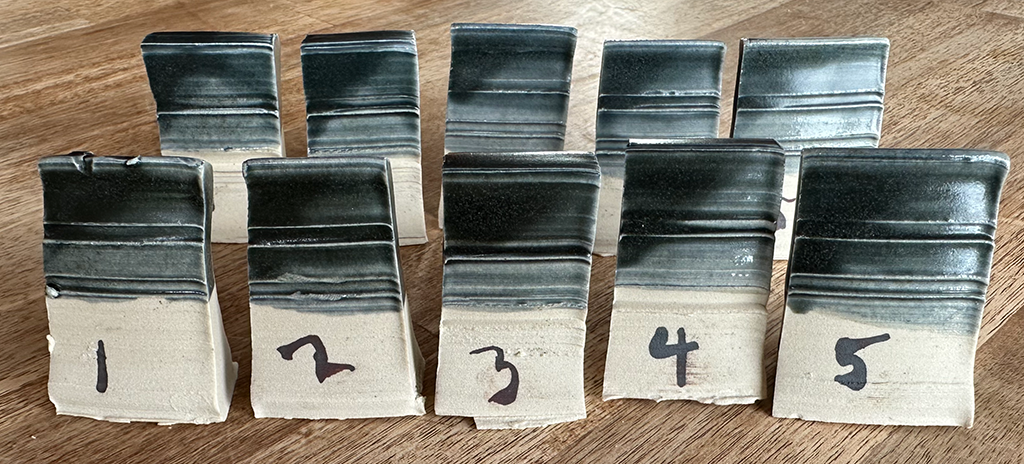
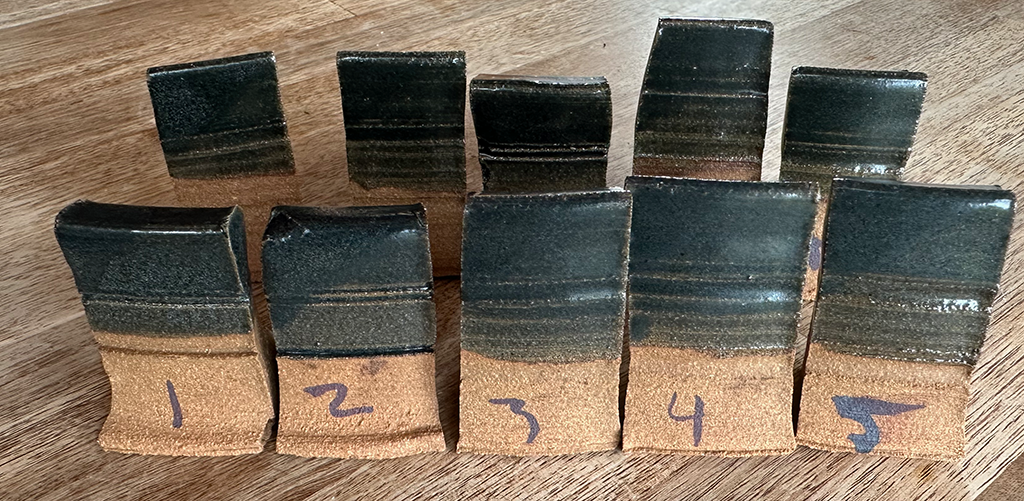
Back Row: Prior, mixed, milled batch, Front Row: Latest, Granodiorite, milled batch (B-mix left and Sedona Red right)
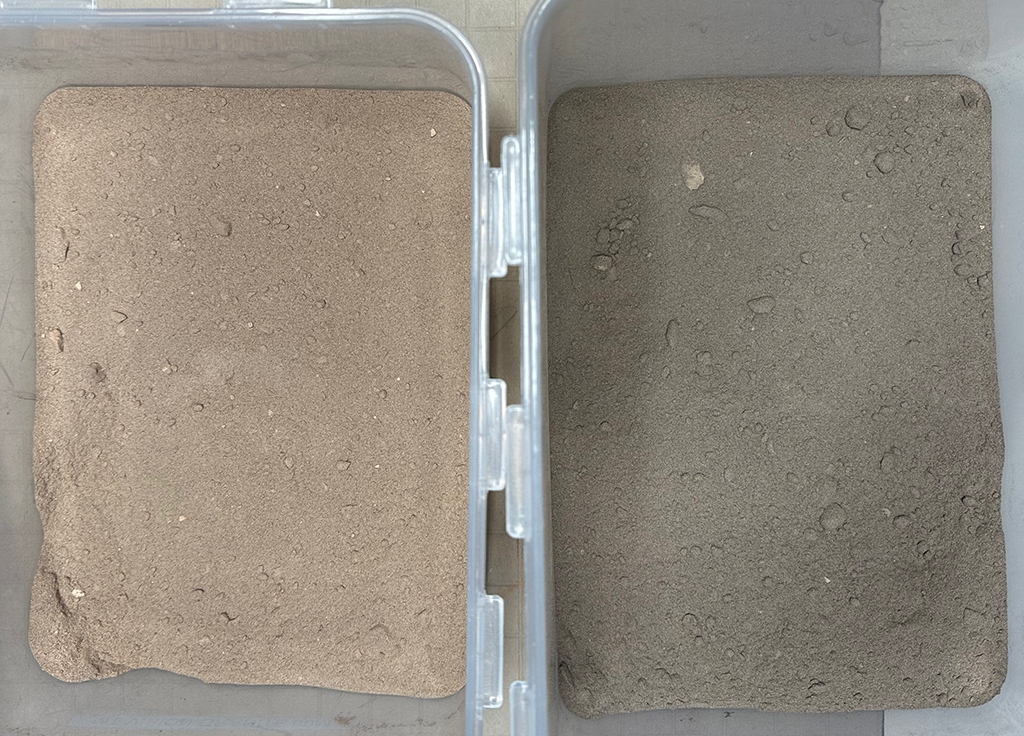
Notes
- There was no appreciable difference between the two mixes of granite (this is good)
- The Boron appears to not have had a visible effect at 5% (Frit 3134)
- The Silica also appears to not have had a large effect at 5%
- All the tiles are pretty consistent and good looking, perhaps expected as the range of variation is small
- The elusive glossy firing, Test 1, remains elusive, but when I want a matte glaze I am good to go
Still stuck in the matte zone, it seems like milling just the granite instead of the granodiorite and testing would be a good approach for trying to get back to Test 1. But the granite can also be simulated by reducing slightly the amount of Wollastonite and adding some Silica. In fact, 70% Granodiorite, 28% Wollasonite and 5% Silica do just this and I plan to test this next.
Test 7
Date:01/12/24
Type: Biaxial 5x5 Blend Tests
Temp: Cone 6
Kiln: Main Kiln (G39)
Clay: B-Mix
Method: Each corner glaze contains 300 gm of material and 250 ml of water, making ~400ml of solution.
The flux corner C is 70% Granite and 30% Wollastonite, the current base receipe. 20 gm of Silica was added to corners B and D and 20 gm of EPK (alumia) was added to corners A and B.
The resulting corner recepies are, in grams
A | B | C | D | |
---|---|---|---|---|
Granite | 183 | 156 | 210 | 174 |
Wollastonite | 78 | 66 | 90 | 75 |
Silica | 0 | 45 | 0 | 51 |
EPK | 51 | 45 | 0 | 0 |
300 | 300 | 300 | 300 |
Then 0.5% of cobalt carbonate (1.5 grams) was added to each corner.
I did blunder again and did not leave enough material in cups B, C and D after blending, so those cells are compromised as are #2 and #24 which suffered from a lack of D's solution for #2 and C's solution for #24. The rest are measured correctly.
I applied the resulting blends to 1 5x5 flat tests and 1 set of 25 self standing test tiles.
The kiln was fired using the normal Kline Cone 6 ramp. The upper portion of the kiln, where the test resided, fired to 30% Cone 7 with Cone 6 surpassed.
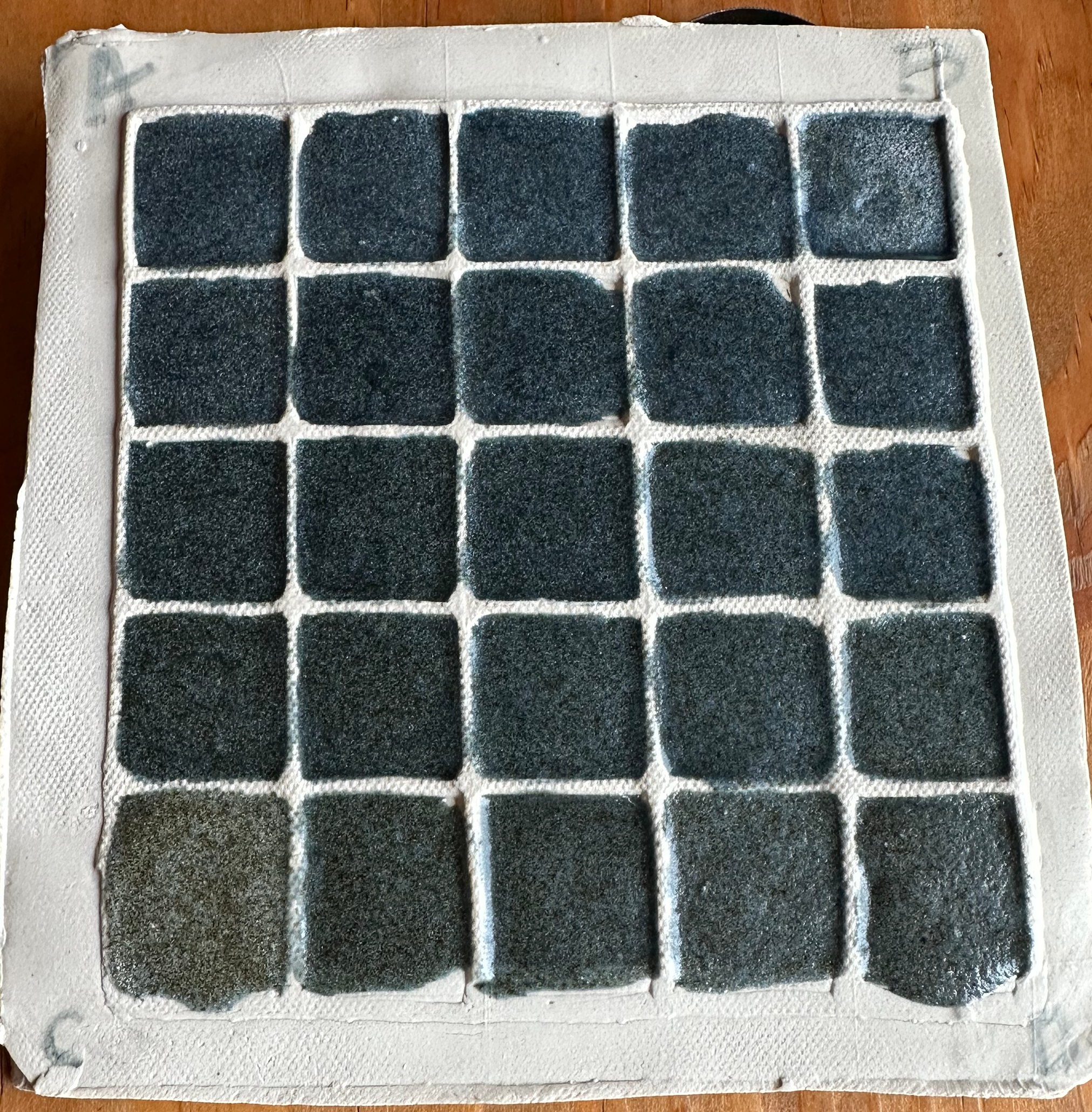
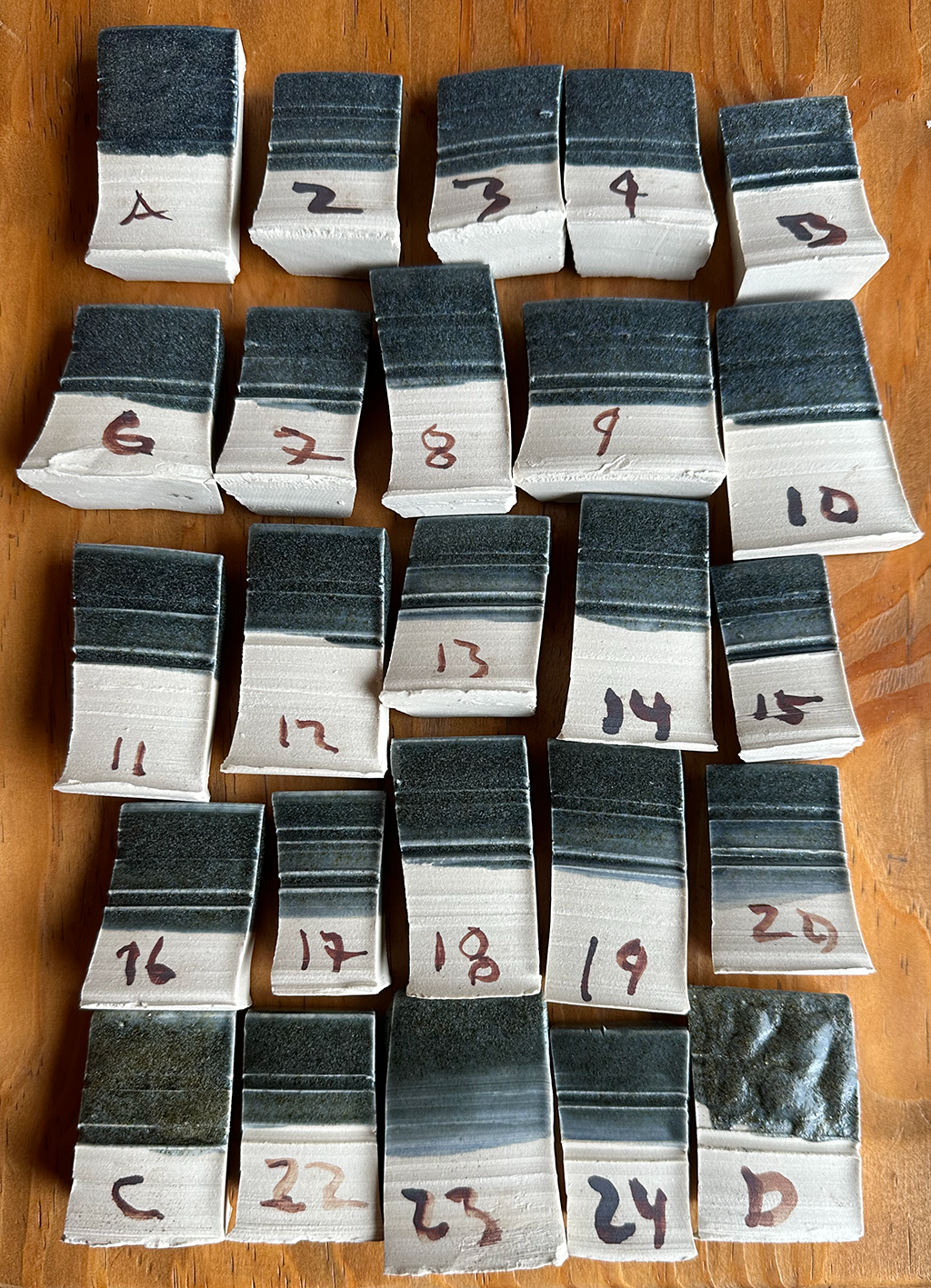
Notes:
While a pretty blue, the result is far from what I expected and I am still trying to understand it. All the cells / tiles came out matte or underfired (they all look underfired to varying degrees, frankly). I was expecting more of a spectrum and hoping to find the glossy glass glaze we saw in Test 1. There is no hint of the glossy eutectic here.
All the other pieces in the same firing, including granite samples, came out as expected, so the reason is not the kiln atmostphere. I did botch the few tiles as mentioned above, but that's irrelevant now.
The milled granite samples are the same as the prior tests, though separately, I am starting to suspect what I collect and how it's milled may be more important than previouslty thought. In other words, at any one time perhaps I don't have material that represents well the chemical analyses I had produced. Then again, I have produced a variety of good results. Sigh.
It is interesting how the gray moves to blue as we increase the silica and alumina. Frankly I cannot really pick a best tile except to perhaps say those in the middle are the "best".
I'm thinking that perhaps I botched the test in a way I didn't notice? I'll have to test again to be sure.
Or, I just might not be in the target area and need to add even more silica to find glossy. Adding Boron would be another good test to drop the melting temperature.
For the record here are the silica / alumina ratios corresponding to the test.
A | 1:6.8 | 1:7.2 | 1:7.7 | 1:8.1 | 1:8.5 | B |
1:7.6 | 1:8.1 | 1:8.6 | 1:9.2 | 1:9.7 | ||
1:8.3 | 1:9.0 | 1:9.6 | 1:10.2 | 1:10.9 | ||
1:9.2 | 1:9.9 | 1:10.6 | 1:11.3 | 1:12.0 | ||
C | 1:10 | 1:10.8 | 1:11.6 | 1:12.4 | 1:13.2 | D |
Test 6
Date:01/04/24
Type: Test Tiles
Temp: Cone 6
Kiln: Test Kiln (T31)
Clay: B-Mix, Red Sedona
Method: A straight comparison of "Tile #22 in Tenmoku Test 7", more Silica, 0.5% Cobalt, SG 1.47 compared to a batch of existing 70/30 - 0.25% and 0.5% Cobalt.
The Tile #22 formula is 67% Granodiorite, 29% Wollastonite, 4% Silica with 0.5% Cobalt and 2% Bentonite added.
Chemically this is a 1:10.3 aliumina / silca ratio with 0.77% Calcium and 0.18% K-Na
Also, for kicks, I refired the 2% Cobalt batch from Test 5, which simulated tile #11 from the Base Test 6. This was an alumina variation rather than a silica one.
Being in the test kiln this gives a chance to compare results in both kilns.
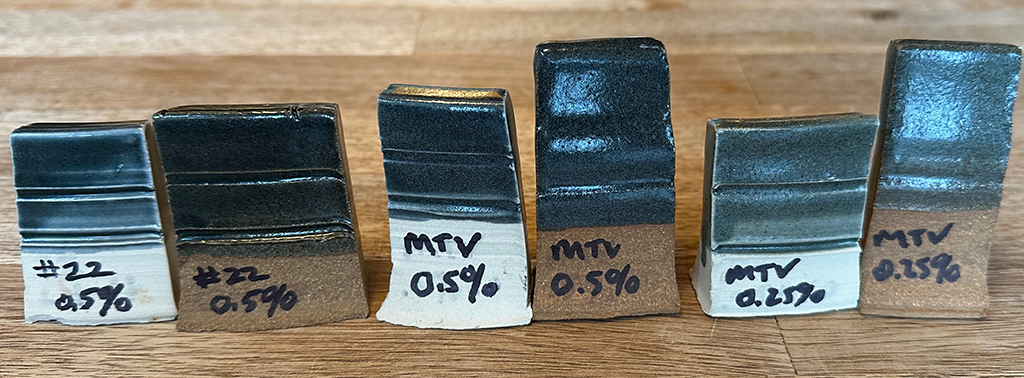
Prior to this test I was not sure why the cobalt formulas were glossy in the test kiln (Test 1) and matte in the main kiln (all other tests, though in review Test 2 below gave me a bit of a heads up).
This test makes it conclusive that differences between the kiln environments are not the cause. Cones placed in each kiln have shown the same temperatures are being produced in both kilns and I now have multiple examples of matte glaze results from both kilns. Cooling regime differences seem to be ruled out as well given these results.
So the cause must be differences in the granite batches. Early on I was mixing the granodiorite with the granite without measure or thought. The granite has 10% more silica than the granodiorite with similar amounts of alumina and KNa (though the calcium is mostly lost in the granite, so less flux).
These latter batches are exclusively granodiorite (though my milling technique is undergoing changes as I firm up the process and this needs to be considered as well).
Regardless, the b-mix tile on the left seems to support more silica will lead back to the eutectic glossy zone found in Test 1. It's still matte, but clearly different. Compare it to Test 1. This is a good result. As a next step a biaxial test needs to be executed.
It remains noteworthing that the Tenmoku versions of essentially the same formulations does not show such variations, while the Base tests mimic the cobalt tests. So the iron oxide is doing something that I don't yet understand - research thus far says it's inert in an oxidation environment?
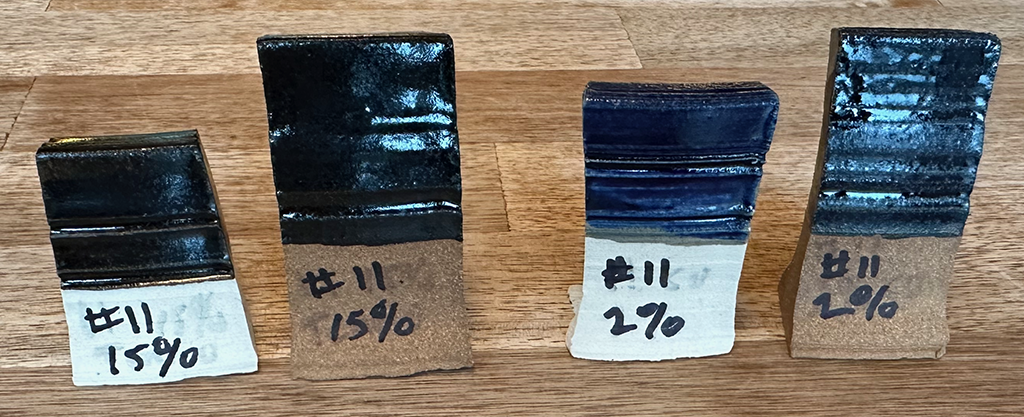
Finally it's worth noting the refire of the alumina enhancement test, which was not very satisfying in Test 5 below was slightly more interesting this time (see the tiles above, left). While I like the Tenmoku result, I'm not sure I would use the cobalt result.
Test 5
Date:12/14/23
Type: Line Blend
Temp: Cone 6
Kiln: Test Kiln (T30)
Clay: B-Mix, Sedona Red
Glaze: 66% Mt. Vision Granodiorite (60M seive) / 28% Wollastonite / 7% EPK + 2% Bendonite
Additive: Colbalt Carbonate
Method: 5 tests of 0.0%, 0.25%, 0.5%, 1% and 2% Cobalt Carbonate by adding 0, 0.5, 0.5, 1.0 and 2.0 gm (cumulative 4 gm) without changing the amount of liquid. 150g material with 150ml water.
I forgot to measure the SG, but it was pretty watery and difficult to apply thickly.
This is a re-do of Test 1 with a different glaze formulation, namely test tile #11 in the base glaze test 6.
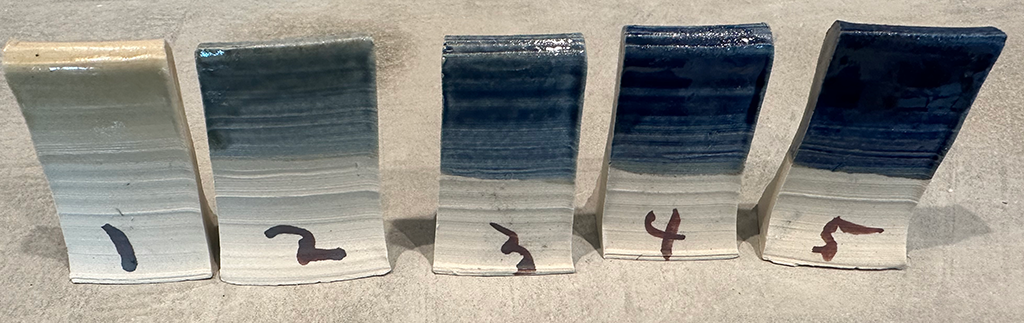
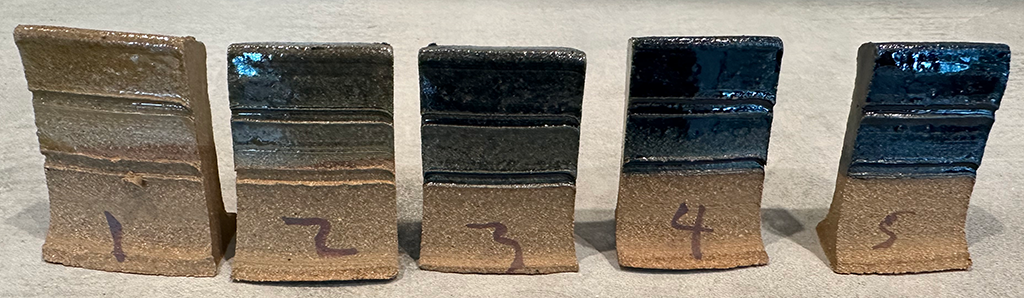
Notes:
I had high hopes for this test since the base glaze biaxial test indicated the addition of the EPK would be an improvement to its quality - it did not.
One issue here is the glaze is too thin, with a lot of its particulant matter falling rapidly to the bottom, but the bigger issue is the glaze does not look fully melted!
One positive is the base glaze without colorant looks nice on the Sedona Red.
Test 4
Date:12/7/23
Type: Main Kiln
Temp: Cone 6
Kiln: Main Kiln (G37)
Clay: Porcelian
Glaze: 70% / 30% Mt. Vision Granite (12hrs milling / 60M seive) / Wollastonite
Additive: Colbalt Carbonate 0.5%
Method: In an attempt to understand better why tests in the test kiln are glossy and tests in the main kiln are sometimes matt, all else being equal, this test places two equal pieces in separate places in the kiln (top (hot), bottom (cool)) to assess the affect, if any, this might have.
Note this problem is more manifest with the colbat tests than the iron oxide tests.
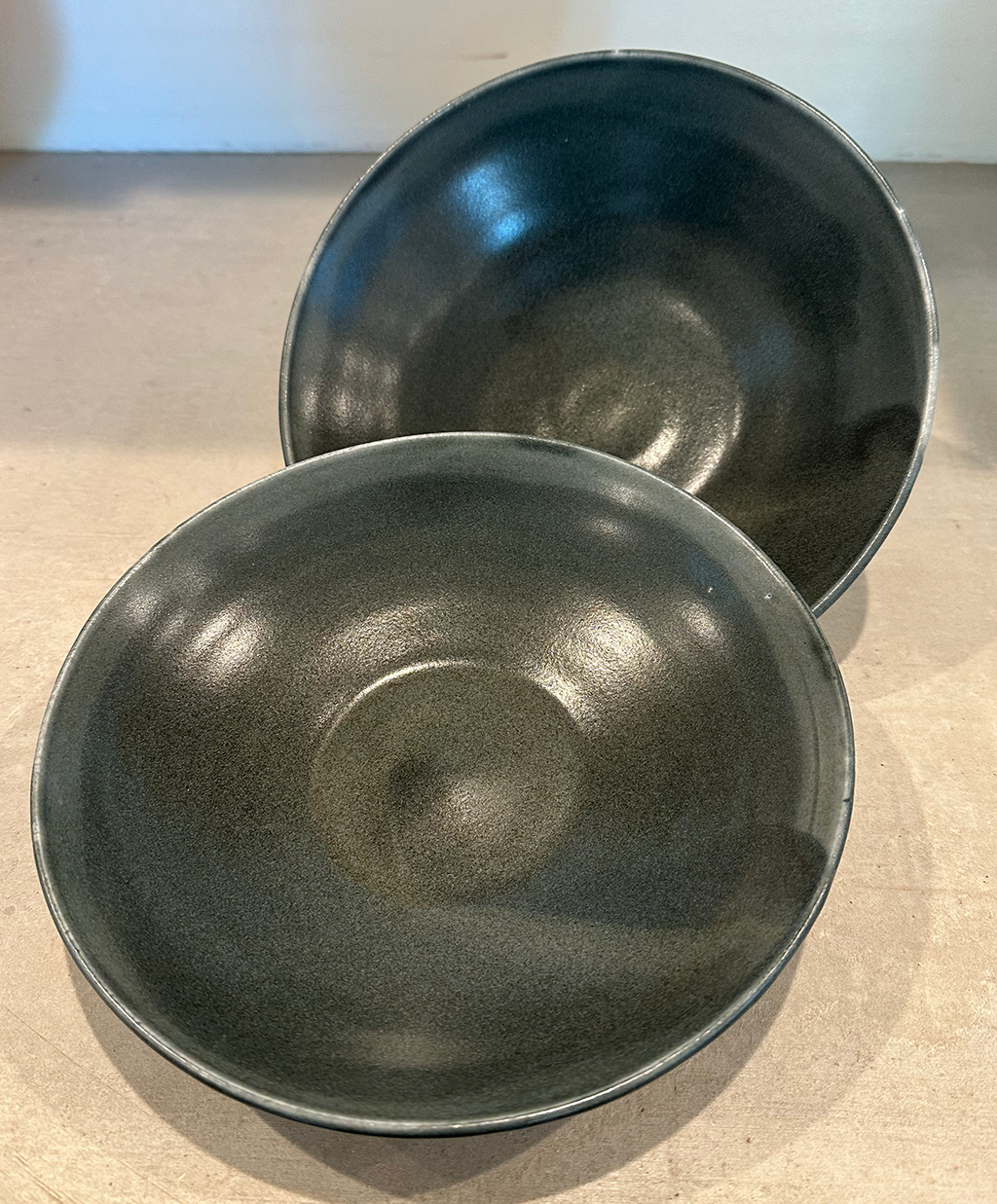
Notes
The recorded temperature difference was just 10% of a cone with the bottom of the kiln recording 25% cone 7 and the top 35% cone 7.
Each piece looks the same and so, in this case anyway, the temperature difference did not make any difference.
The glaze is matt and opaque. It needs to be applied thickly and is difficult to apply evenly. Contrast this result with Test 1 below from the test kiln. The result is consistent with other tests in the main kiln.
Test 3
Date 11/14/23
Type: Test Tiles
Temp: Cone 6
Kiln: Main Kiln (G36)
Clay: B-Mix, Dark Red, Sedona Red
Glaze: Mt Vision Base Glaze, SG 1.5
Additive: Cobalt Carbonate 0.5%
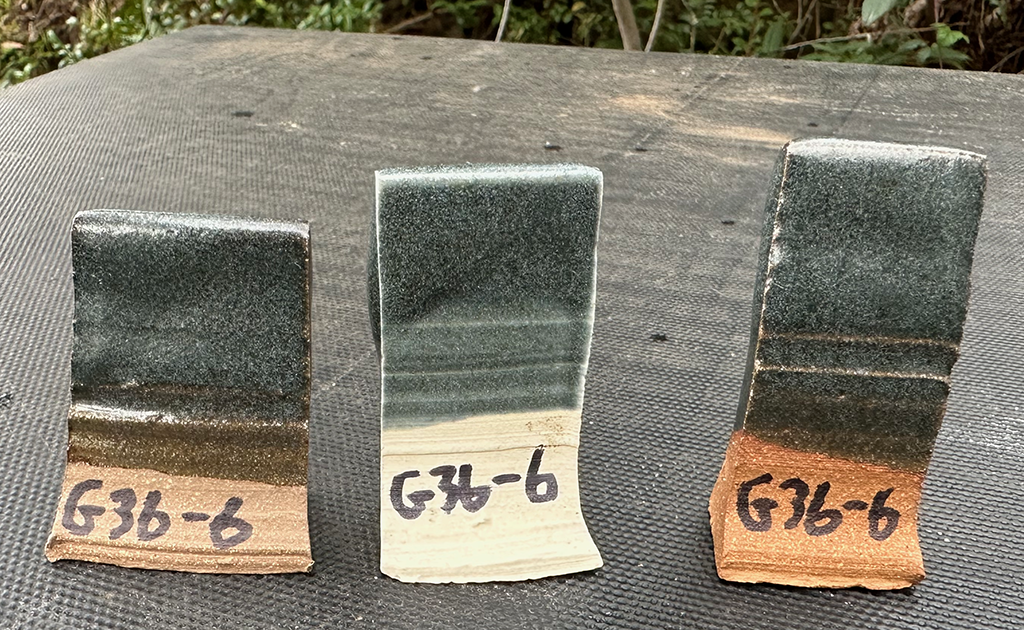
Notes:
Also from a new batch of granite, these tests exhibit the matte seen in Test 2 and not the gloss we see in Test 1. But an interesting glaze none-the-less. I would like to find a way to move from the matte to gloss to matte just to understand the chemistry better.
Test 2
Date 10/3/23
Type: Test Tiles
Temp: Cone 6
Kiln: Test Kiln (T29)
Clay: B-Mix, Dark Red, Sedona Red
Glaze: Mt Vision Base Glaze, SG 1.42
Additive: Cobalt Carbonate 0.25%
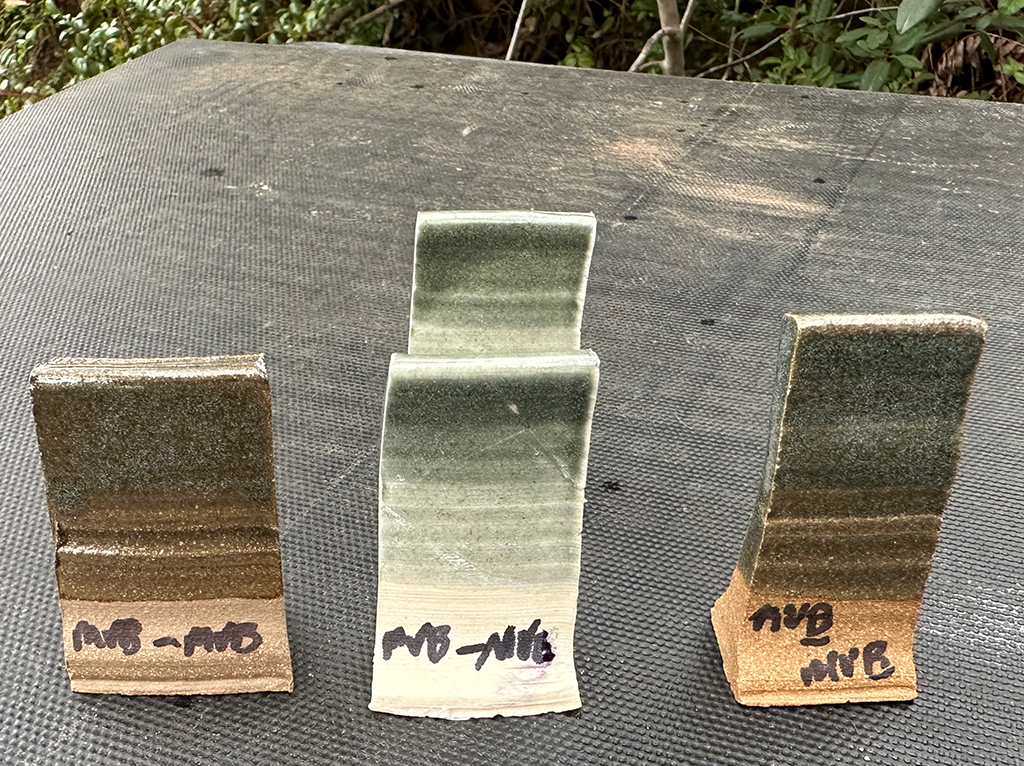
Notes:
While beautiful, this is very different than Tile 2 in Test 1. It does come from a newly mixed batch of granite. The matte finish is reflected in the sea-grey bowls presented above while the deep blue bowl, also above, comes from glaze mixed for Test 1.
I was wondering if the main kiln was firing differently from the test kiln, but here we find a matte version in the test kiln, different from Test 1, and also, the extra B-Mix tile in the back is a copy fired in the main kiln and it looks just the same.
So I suspect a difference in the granite mixture and implies I need to take more care how I mix the two types of granite found on the property (see here)?
Test 1
Date 9/14/23
Type: Test Tiles
Temp: Cone 6
Kiln: Test Kiln (T28)
Clay: B-Mix
Glaze: Mt Vision Base Glaze, SG 1.43, 200ml batch
Additive: Cobalt Carbonate
Method: 5 tests of 0.0%, 0.25%, 0.5%, 1% and 2% Cobalt Carbonate by adding 0, 0.5, 0.5, 1.0 and 2.0 gm (cumulative 4 gm) without changing the amount of liquid.
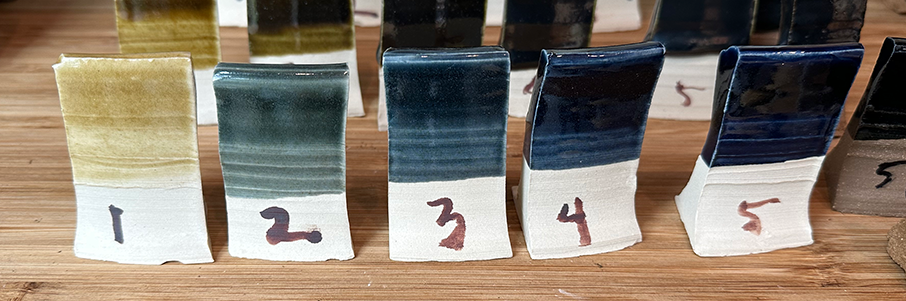
MV Base | |||||
---|---|---|---|---|---|
Cobalt Carbonate | 1 | 2 | 3 | 4 | 5 |
Added | +0g | +0.5g | +0.5 | +1.0g | +2.0g |
Cumulative | +0g | +0.5g | +1.0g | +2.0g | +4.0g |
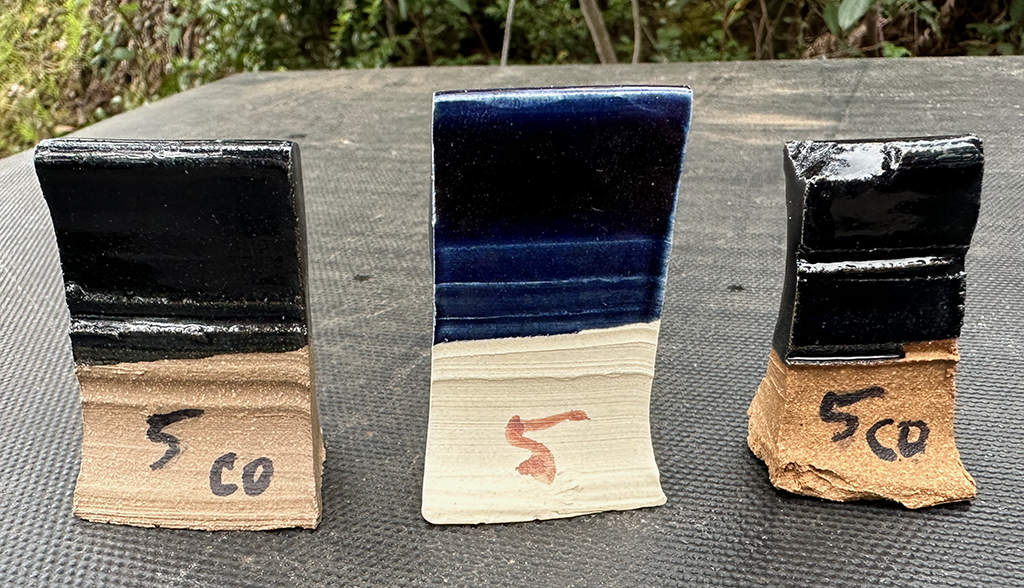
Notes:
I was delighted by these tests.
1- Fine example of the base glaze
2- Very attractive, want to explore
3- Very attractive, want to explore
4- Very attractive, want to explore
5- Very dark, interesting but perhaps better thinner unless seeking a very dark blue. Example given in the picture gallery above.